Бережливое производство. Часть 2 + 6 сигм
- Джимшер Челидзе
- 11 сент. 2021 г.
- 11 мин. чтения
Обновлено: 13 сент. 2022 г.
Содержание:
Это 2-й пост про бережливое производство. В нем мы рассмотрим некоторые инструменты бережливого производства, а также что такое 6 сигм и Lean 6 Sigma.
1-я часть доступна по ссылке
Один из инструментов бережливого производства, наряду с SIPOC. Value Stream Mapping — это инструмент, который визуализирует процесс превращения сырья в готовую продукцию, отпускаемую потребителям. Его объекты — материальные и информационные потоки ресурсов, а также время.
Создание Value Stream Mapping делится на три блока:
Производственный или процессный поток — традиционная блок-схема, в которой слева направо фиксируется путь создания ценности начиная закупкой сырья и заканчивая отгрузкой продукции. Если кроме основного процесса существуют дополнительные или вспомогательные, они наносятся под основным. Таким образом основные задачи отделяется от второстепенных.
Информационный или коммуникационный поток — в верхней части карты потока создания ценности стрелками изображаются потоки информации, которые происходят параллельно с производством. Учитывается и формальный и неформальный обмен данными. Информационные потоки наносятся на карту в свободной форме, так, как они протекают в действительности.
Timeline и расстояния — линии, которые рисуются в нижней части карты. Линия времени делится на верхнюю и нижнюю части. Сверху отображается lead time — время ожидания. Снизу наносится продолжительность цикла. Под линией времени может находиться еще одна линия, в самом низу, показывает расстояния, по которым продукт или персонал движутся внутри процесса.


Упрощенный алгоритм работы:
Шаг 1. Выбор процесса для систематизации потока ценности (подготовительный)
Шаг 2. Символы Value Stream Mapping
Шаг 3. Определение границ процесса
Шаг 4. Шаги процесса
Шаг 5. Добавление информационных потоков на карту
Шаг 6. Добавление данных о каждом шаге процесса
Шаг 7. Подсчет запасов
Шаг 8. Добавление хронологии процесса — Timeline
Шаг 9. Карта будущего состояния
Шаг 10. План для внедрения улучшений
Полезные ссылки:
Видео
Poka-yoke (пока-ёкэ) - один из инструментов бережливого производства. На русском он звучит как «защита от дурака».
Устройства защиты от дурака предохраняют не просто от ошибок, а от ошибок, вызванных человеческим фактором:
невнимательностью
забывчивостью
неосторожностью
незнанием
усталостью
и даже саботажем.
Люди ошибаются, а poka-yoke приспособления не дают им допустить ошибку.
Принцип действия poka-yoke характеризуются:
стопроцентным охватом проверки
быстрой обратной связью
низкой стоимостью и простотой.
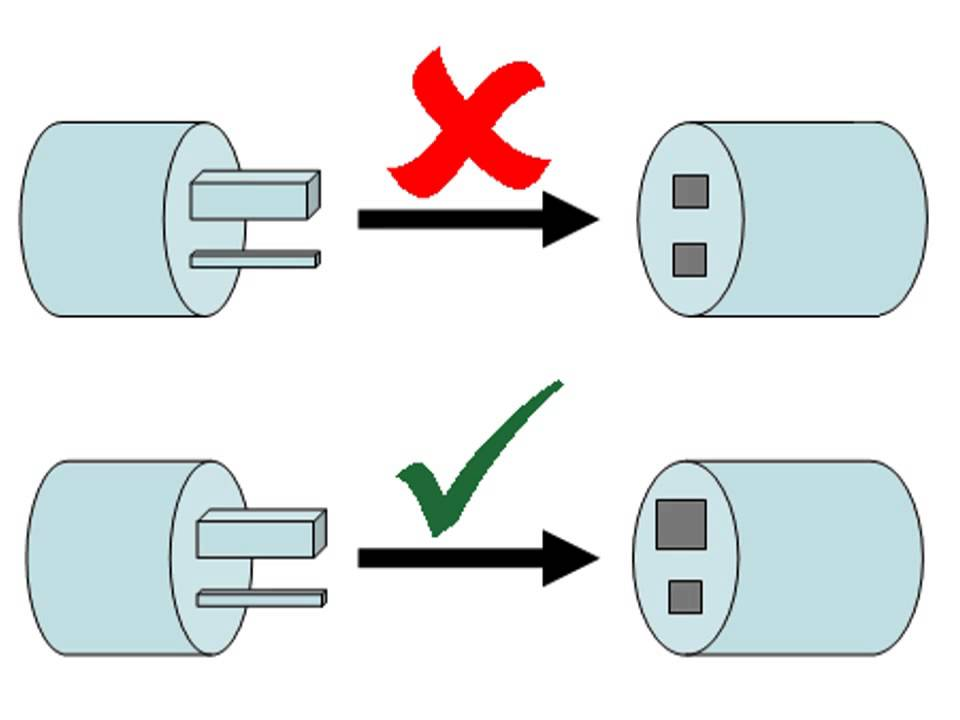
Устройства poka-yoke работают по принципу не пропустить ни одного дефекта.
Они регулируют производственный процесс и предотвращают дефекты одним из двух способов:
Система контроля — останавливает оборудование, когда возникает нарушение нормы, или блокирует заготовку зажимами, чтобы она не двигалась дальше по конвейеру, пока не будет обработана как требуется. Это более предпочтительная система, поскольку она не зависит от оператора.
Система предупреждения — посылает оператору сигнал остановить машину или устранить проблему. Зависит от оператора, поэтому человеческий фактор не полностью исключен.
Poka-yoke не ищет виновных в ошибках, цель — найти и устранить слабые места в производственной системе, из-за которых ошибка стала возможной.
Способы защиты от дурака делятся на 3 уровня по возрастанию эффективности:
1-й уровень — обнаруживает несоответствие деталей или продукции. Система обнаруживает дефектную деталь, но не отбрасывает её.
2-й уровень — не допускает несоответствие. Система не дает обработать дефектную деталь на следующей стадии производственного процесса.
3-й уровень — конструкционная защита, например, изделие имеет такую конструкцию, что установить или собрать его непредусмотренным образом невозможно.
Принципы защиты от ошибок
Устранение: этот метод устраняет возможность ошибки путем редизайна продукта или процесса так, чтобы проблемная операция или деталь вообще больше не требовались. Пример: упрощение продукта или соединение деталей, чтобы избежать дефектов продукта или сборки.
Замещение: чтобы повысить надежность, нужно заменить непредсказуемый процесс на более надежный. Пример: Использование роботизации и автоматизации, чтобы предотвратить ошибки ручной сборки. Применение автоматических диспенсеров или аппликаторов для точной дозировки жидких материалов.
Предупреждение: инженеры-конструкторы должны разработать такой продукт или процесс, чтобы вообще невозможно было совершить ошибку. Пример: Конструктивные особенности деталей, которые допускают только правильную сборку; уникальные разъемы для избежания неправильного подключения кабелей; симметричные детали, которые позволяют избежать неправильной установки.
Облегчение: Использование определенных методов и группирование шагов облегчают выполнение процесса сборки. Пример: Визуальные элементы управления, которые включают цветовое кодирование, маркировку деталей. Промежуточный ящик, который визуально контролирует, чтобы все детали были собраны. Нанесение характеристик на детали.
Обнаружение: Ошибки обнаруживаются до того, как они перейдут на следующий производственный процесс, чтобы оператор мог быстро исправить проблему. Пример: Сенсорные датчики в производственном процессе, которые определяют, что детали собраны неправильно.
Смягчение: Старание уменьшить влияние ошибок. Пример: Предохранители для предотвращения перегрузки цепей в результате коротких замыканий.
Акцент контроля качества смещается с проверки готовой продукции на факт брака на предупреждение возникновения брака на каждом этапе производства.
«Дом TPS» был разработан Таичи Оно и И. Тойода специально для того, чтобы упростить объяснение сути производственной системы Тойоты служащим и поставщикам. По словам разработчиков, форма дома (крыша, колонны и основание) была использована преднамеренно, потому что она понятна каждому и символизирует стабильность и основательность.
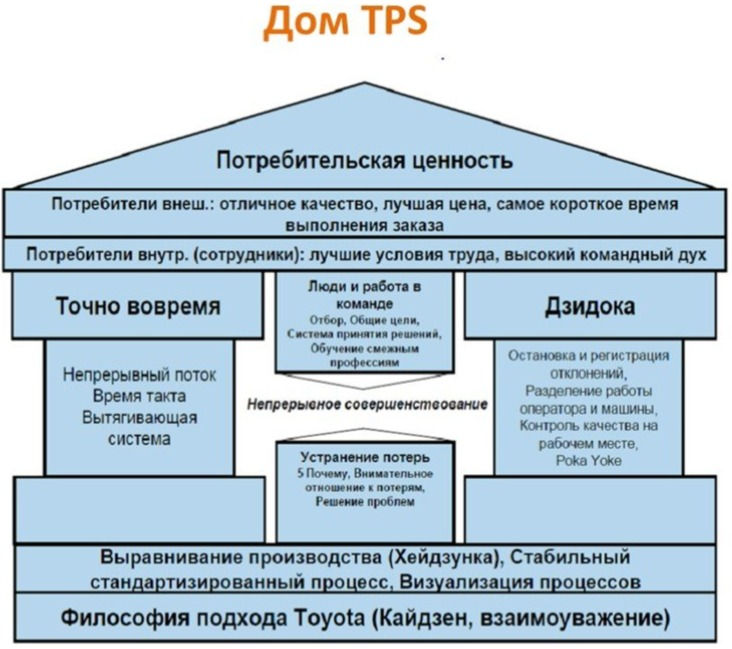
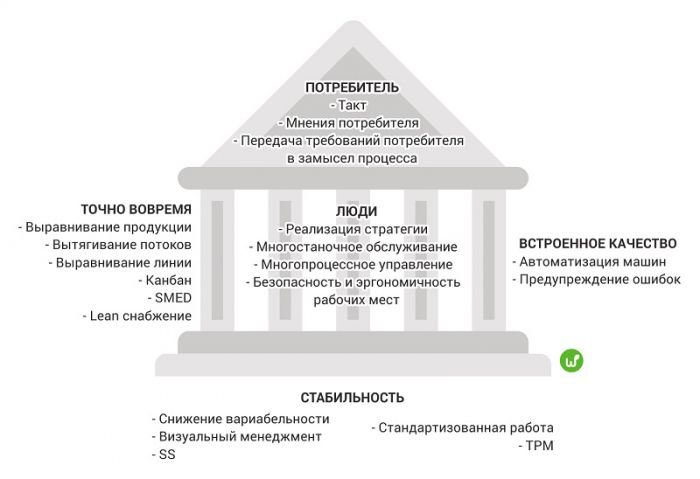
1-е место — Несоответствие ценностям Бережливого Производства
2-е место — Низкий приоритет у руководства
3-е место — Формалистика (формальный подход)
4-е место — Следование моде
5-е место — Проблемы целеполагания и видения будущей производственной системы
6-е место — Инструментальный (технический) подход.
7-е место — Нехватка ресурсов.
8-е место — Недостатки в организации и управлении внедрением Бережливого Производства
9-е место — Плохие базовые условия для сотрудников
10-е место — Нехватка компетенций
Плюсы БП

Недостатки бережливого производства
Проблемы питания / снабжения
Из-за ограниченности запасов на складах, бережливое производство во многом зависит от поставщиков, которые могут предоставлять продукцию для производственного процесса ненадежно и с перебоями. Такие проблемы, как болезнь сотрудника, задержки с транспортировкой и ошибки со стороны поставщиков могут быть фатальными. Продавцы могут быть неспособны или даже не иметь желания поставлять детали или изделия по жесткому графику или в меньших количествах. Такие требования могут стать бременем для поставщиков с накладными затратами и создать напряженность, которая в конечном итоге повлияет на производственный процесс и может привести к частой смене поставщиков или даже к трудностям с их поиском.
Высокие затраты на внедрение
Реализация бережливого производства часто означает полный демонтаж предыдущих физических установок завода и систем. Обучение сотрудников может быть длительным и приобретения менеджерами опыта в Lean может прибавить расходы компаний. Приобретение оборудования и его настройка может затянуть процесс внедрения. Малый и средний бизнес, в частности, может счесть стоимость переход к бережливому производству непомерно высокой.
Сопротивление сотрудников
Lean требуют капитального ремонта производственных систем, которые могут вызвать стресс и отказ от работы сотрудников, которые предпочитают старые способы ведения дел. Кроме того, бережливое производство требует ввода постоянного сотрудника по контролю качества. Пожилые работники могут предпочитать предыдущие методы и могут оказывать сопротивление работе группы. В данном случае, хорошие менеджеры имеют решающее значение для перехода к бережливому производству. Это тоже определенная трудность — поиск менеджеров с достаточным руководством и навыками убеждения и работы с сопротивлением.
Проблема неудовлетворенности клиентов
Так как производственный процесс настолько сильно зависит от эффективности поставщиков, любое нарушение в цепи поставок — и, следовательно, на производстве — может стать проблемой, которая отрицательно сказывается на клиентах. Задержка доставки может привести к длительным маркетинговым проблемам, которые сложно будет преодолеть.
6 сигм - это американский подход к управлению производством, ориентированным на решение проблем и снижение количества брака до уровня 3,4 единицы на 1 млн единиц готовой продукции.
Концепция родилась в компании Motorola.

Суть концепции сводится к необходимости улучшения качества выходов каждого из процессов, минимизации дефектов и статистических отклонений в ежедневной деятельности. Концепция использует методы управления качеством, в том числе, статистические методы, требует использования измеримых целей и результатов, а также предполагает создание специальных рабочих групп на предприятии, осуществляющих проекты по устранению проблем и совершенствованию процессов («чёрные пояса», «зелёные пояса»).
ПРИМЕНЕНИЕ 6 СИГМ ПОЗВОЛЯЕТ ВЫДЕЛИТЬ ГРАНИЦЫ УПРАВЛЯЕМОГО ПРОЦЕССА. А В СЛУЧАЕ ВЫЯВЛЕНИЯ ПРОБЛЕМЫ ПОНЯТЬ, ГДЕ СИСТЕМНАЯ ПРОБЛЕМА, А ГДЕ ЧАСТНЫЙ СЛУЧАЙ. ЧТО ПОЗВОЛЯЕТ НЕ ЛЕЧИТЬ ФОРС-МАЖОР ИЗЛИШНИМИ МЕРАМИ В ОТНОШЕНИИ ВСЕЙ СИСТЕМЫ. А ТАКЖЕ ПОЗВОЛЯЕТ ВЫЯВИТЬ БЛАГОПРИЯТНЫЕ СОБЫТИЯ, ПРОАНАЛИЗИРОВАТЬ ИХ И ВНЕДРИТЬ ДЛЯ УЛУЧШЕНИЯ ПРОЦЕССА В ЦЕЛОМ.
Ориентироваться на пользователя
Например, учитывать целевую аудиторию сайта и следить за удобством интерфейса.
Принимать решения на основе данных и фактов
Никаких предположений. Все должно быть подкреплено цифрами. Для этого нужно определить важные для компании показатели и следить за ними.
Процессный подход
Смотреть, как взаимодействуют процессы в компании. Например, тестировать каждую новую функцию сайта сразу после ее создания — дешевле. А в конце проекта — дороже. Плюс можно не успеть уложиться в сроки.
Просчитывать ходы
Учитывать возможные результаты и их последствия. Например, если уровень отклонений один, чтобы его улучшить, понадобится дополнительное время на тестирование. Это может не устроить заказчиков.
Сотрудничество внутри команды
Иметь общую цель и помогать друг другу в ее достижении.
Рисковать
Не бояться потерпеть неудачу ради возможности стать лучше.
Сигма (σ) — буква греческого алфавита. В математике ей обозначают стандартное отклонение, то есть когда данные не соответствуют среднему значению.
Правило 3 сигм гласит: практически все значения нормально распределённой случайной величины лежат в интервале +- 3 сигм от среднего значения. То есть приблизительно с вероятностью 0,9973 значение нормально распределённой случайной величины лежит в указанном интервале.


Алгоритм расчета 6 сигм:
Складываем все измеренные значения и рассчитываем среднее арифметическое значение
Считаем разность между максимальным и минимальным значением, например за месяц
Считаем такую же разность за еще, например, 5 месяцев
Считаем среднее арифметическое этой разницы за 6 месяцев
В контрольных картах Шухарта находим показатель d2, и берем значение для выборки, в нашем примере это 6 месяцев, значит d2 = 2,534
Берем нашу среднюю разницу между максимум и минимум и делим на d2
Получаем сигму
Теперь от среднего значения из пункта 1 откладываем 3 сигмы вверх и вниз. Получаем 6 сигм, которые показывают границы нашего управляемого процесса. Что не внутри - это отклонения. Выясняем причины и работаем с ними

Контрольная карта Шухарта — визуальный инструмент, применяемый в управлении производством и бизнес-процессами. График изменения параметров процесса во времени для осуществления статистического контроля стабильности процесса.
Своевременное выявление нестабильности позволяет получить управляемый процесс, без чего никакие улучшения невозможны в принципе. Контрольные карты впервые введены в 1924 году Уолтером Шухартом с целью снижения вариабельности процессов путём исключения отклонений, вызванных несистемными причинами.
При введении контрольных карт в организации важно определить первоочередные проблемы и использовать карты там, где они наиболее необходимы. Сигналы о проблемах могут исходить от систем управления дефектами, от претензий потребителей, от любых процессов организации.
Контрольные границы — коридор, внутри которого лежат значения при стабильном состоянии процесса. Контрольные границы рассчитываются по формулам, жестко привязанным к типу карты; эти границы вычисляются по данным о процессе, и никак не связаны с допусками:
CL — центральная линия (обычно среднее значение или медиана по некоторому объёму данных),
LCL — нижняя контрольная граница,
UCL — верхняя контрольная граница.

Признаки особой изменчивости сигнализируют о нарушении стабильности (управляемости) процесса:
выход точек за верхнюю или нижнюю границы контрольной карты,
7 или более точек подряд лежат по одну сторону от средней линии,
более 6 точек монотонно возрастают или убывают.
Есть и другие признаки, но установившегося общепринятого набора дополнительных правил чтения контрольных карт нет, поэтому рекомендуется использовать в первую очередь правило Шухарта (выход точек за границы), а все прочие вводить по мере накопления опыта при необходимости.
По шкале измерения карты подразделяются на качественные и количественные. Среди возможных вариантов по выборочному параметру — карты индивидуальных значений, скользящих размахов, среднего, среднеквадратического отклонения, медианы, размаха.
DMAIC (аббревиатура от англ.define, measure, analyze, improve, control — определение, измерение, анализ, совершенствование, контроль) — один из главных инструментов 6 сигм. Это подход к последовательному решению проблем и совершенствованию бизнес-процессов
DMAIC, как и большинство методологий совершенствования основаны на цикле Деминга — PDCA
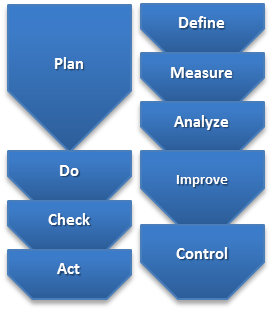
Cогласно DMAIC, решение каждой задачи улучшения процесса или устранения проблемы должно последовательно пройти через все фазы:
Первая - ограничения. Необходимо определить заказчиков, обоснования проекта, рамки, цели и временные границы проекта:
Вторая - измерения. Определяются основные метрики проекта, надёжность источника данных, актуальное состояние процесса.
Третья - анализ. Исследования возможностей процесса, причин проблемы, возможных рисков.
Четвертая - совершенствование. Осуществляется модификация процессов и систем, структурная декомпозиция работ.
Пятая - контроль. Поддержание изменений процессов, подготовка отчётов и закрытие проекта.
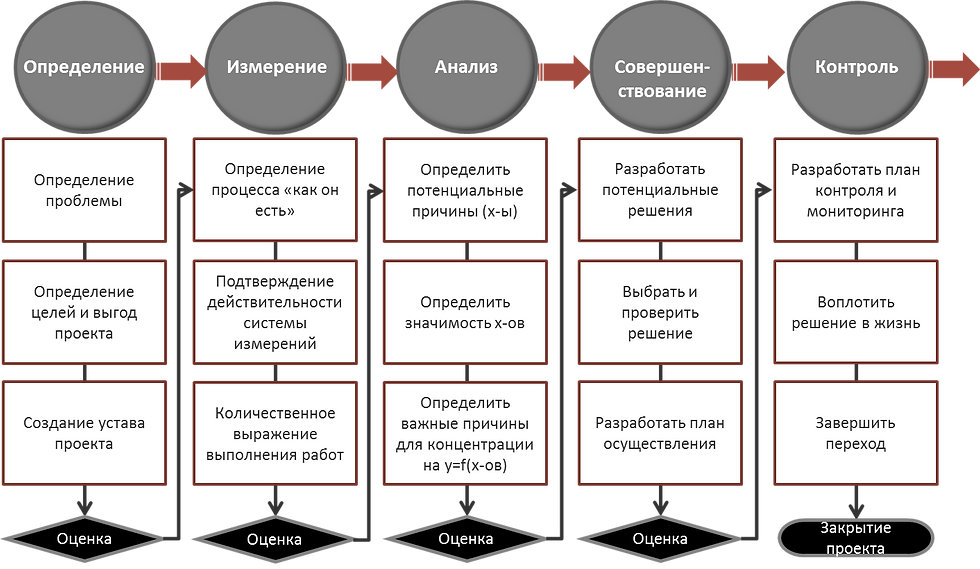
Считается, что именно такая последовательность обеспечивает структурированный подход, позволяющий двигаться от определения сути проблемы к внедрению решений.

SIPOC (supplier, input, process, output, customer — поставщик, вход, процесс, выход, заказчик) — один из инструментов описания бизнес-процессов. SIPOC позволяет проследить бизнес-логику процесса, с высоким, но управляемым уровнем абстракции.

Карты SIPOC применяют:
в проектах 6 сигм на первой стадии DMAIC — Define – для того, чтобы определить “рамки” проекта. С помощью SIPOC устанавливают границы рассматриваемого процесса перед тем, как приступить к его измерению (Measure) и анализу (Analyze).
в проектах Lean ("Бережливое производство") на этапе поиска потерь для того, чтобы описать движение информации/товаров/услуг, а так же взаимоотношений, возникающих между участниками бизнес-процесса.
для реорганизации бизнес-процессов, их непрерывного совершенствования. Многие проблемы в компаниях возникают на стыках подразделений и должностей. Здесь хорошо помогает реализованная в SIPOC концепция «клиент – поставщик» – одна из основ процессного подхода.

Суть метода SIPOC заключается в том, что мы:
Особое внимание уделяем «масштабу» процесса.
Разбираем процесс, начиная от потребителей конечного результата процесса, заканчивая его инициатором. Не наоборот!
Особое внимание уделяем «стыкам» этапов процесса.
Особое внимание уделяем читабельности карты процесса
Начинайте формировать SIPOC “справа” (C->O->P->I->S):
Определите заказчиков.
Опишите продукты или услуги, которые требуют заказчики.
Приведите краткое (5-7 ключевых операций) описание процесса.
Укажите основные входы процесса.
Приведите перечень ключевых поставщиков
Если для работы над существующими процессами применяют цикл DMAIC, то для разработки новых процессов, систем, продуктов или услуг специалисты 6 сигм чаще всего применяют другой цикл – DMADV:
Определение.
Измерение.
Анализ.
Дизайн или разработка.
Верификация.
DMADV может служить каркасом отдельно взятого проекта или же дорожной картой организации в сфере конструирования, разработок и инноваций. При этом значительная часть инструментария может быть заимствована из классического подхода шести сигм (DMAIC) и смежных методологий (проектного менеджмента, реинжиниринга и т.д.).
Алгоритм DMADV также может упоминаться как DMADOV, где дополнительная «O» означает «Оптимизировать»:
1. Define - Определение - определить цели проекта, аналогичные DMAIC.
2. Measure - Измерение – Измерить ожидания клиентов. Также Вам нужно провести сравнительный анализ и бенчмаркетинг (анализ конкурентов).
3. Analyze - Анализ - Поиск и анализ альтернативных решений
4. Design - Дизайн - Проведение детального проектирования
5. Optimize - Оптимизация - Использование проектов, бизнес-кейсов для оптимизации решения
6. Verify – Проверка - Проверить дизайн с помощью пилотных тестов, перед запуском продукта.
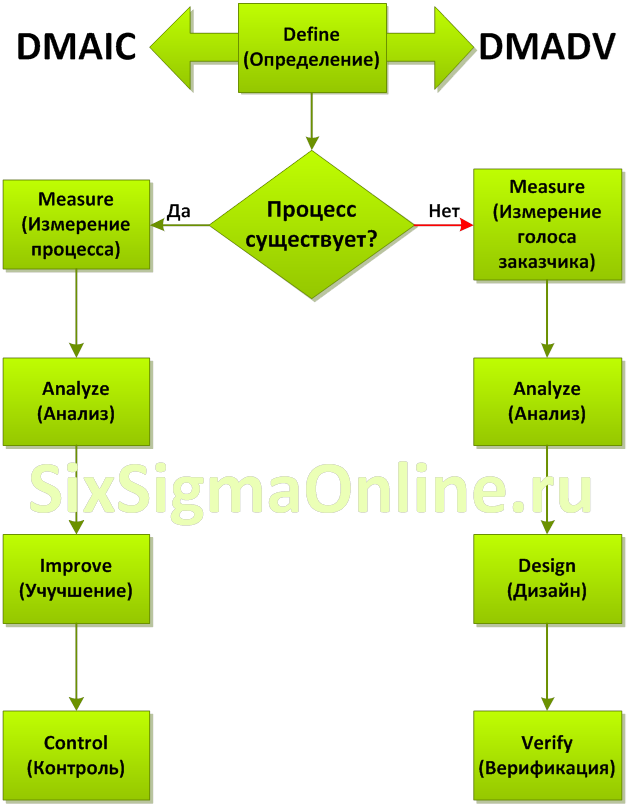
Белые пояса и Желтые пояса — сотрудники компании, которые знают Шесть Сигм на начальном уровне и частично помогают или участвуют в проекте.
Новички, обладающие только теоретическими знаниями, получают статус Белого пояса.
Зеленые пояса — это сотрудники, которые помимо своих должностных обязанностей работают над внедрением методологии, оптимизацией бизнес-процессов. Следят за этим Черные пояса
Черные пояса занимаются проектом и выполняют порученные им задания
Мастера черного пояса контролируют внедрение Шести Сигм и командуют обычными Черными поясами
Чемпионы внедряет методологию в организации и наставляет обладателей Черных поясов
Главное руководство. Оно распределяет обязанности и ресурсы. Главное руководство устраняет внутрикорпоративные барьеры и борется с прирожденным сопротивлением персонала к изменениям
Lean Six Sigma – это общая система, которая включает в себя и японскую, и американскую концепции, объединяя в себе их самые эффективные и результативные методы и инструменты:
Бережливое производство (или Lean manufacturing) — действия, направленные на сокращение потерь и ускорение процессов.
6 сигм (или Six Sigma) — действия, назначение которых — повышение качества и увеличение удовлетворенности и лояльности клиентов.

У каждой из этих концепций есть преимущества и недостатки - так вот система Lean Six Sigma объединяет их и включает в себя все преимущества обеих концепций и восполняет недостатки каждой (то, что упускается в одной концепции, есть во второй). Чтобы визуально проще было это увидеть, посмотрите таблицу сравнительного анализа этих концепций.



Практика использования концепции Lean Six Sigma на западных предприятиях позволяет собственными силами в короткие сроки (около года) добиться результатов:
снижение себестоимости продукции и услуг на 30-60%;
сокращение времени предоставления услуг до 50%;
сокращение количества дефектной продукции примерно в 2 раза;
повышение без дополнительных затрат объема выполненных работ до 20%;
снижение стоимости проектных работ на 30—40%;
сокращение времени выполнения проектов до 70%.
Ссылки:
Видео:
Бережливое производство и 6 сигм - не единственные системы в менеджменте. Она отлично сочетается с теорией ограничения систем, проектным управлением, цифровой трансформацией и т.п.

Ну и самым терпеливым - описание производственной системы Росатома как примера использования инструментов бережливого производства