Theory of systems limitation
- Джимшер Челидзе
- May 14, 2024
- 9 min read
Updated: Jul 8, 2024
Content
In the work of efficiency improvement and transformation, not only change and technology are important, but also the point of application of efforts.
For clarity, let's look at a practical example.
You need to increase the productivity of a plant, for example, for the production of metal doors.
You can approach this question:
By reducing internal costs and increasing productivity through labor organization
Through increased productivity during modernization and technical re-equipment
Let’s say that organizational activities have exhausted their potential. You have digitized and visualized your processes, eliminated all losses, calculated the productivity of departments and identified the limitation of your system - the painting shop.
Then you turned to your industrialists and they brought a list of what needs to be modernized.
According to preliminary calculations, to modernize the workshop you need $2 million and the workshop productivity will increase by 40%, and the percentage of defects will decrease by 80%. Cumulatively, this will increase your overall productivity by 60%.
Next, you visualized the flows in production, simulated all the scenarios, depending on the product line, and found the limitation of the system already inside the workshop.
The principles of lean manufacturing (Tahiti Ono circle, elimination of waste) and mathematical modeling will help with this.
As a result, you saw that you can invest only $1 million and the productivity of the workshop will increase by 35%, and the percentage of defects will decrease by the same 80%. The overall productivity of the enterprise will increase by 53-55%.
This is the principle of systems limitation theory.
And so, systems limitation theory is a management methodology developed by Eliyahu Goldratt. The essence of the theory is that the effectiveness of any work depends on the ability to find and manage restrictions - the “bottlenecks” of the system. Modern interpretations highlight TOC as a method of focusing resources on solving a specific problem, focusing on which will achieve a significantly greater effect than in the case of simultaneous work on several problems.
And sometimes, to improve the performance of the entire system, it is necessary to reduce the performance of individual elements.
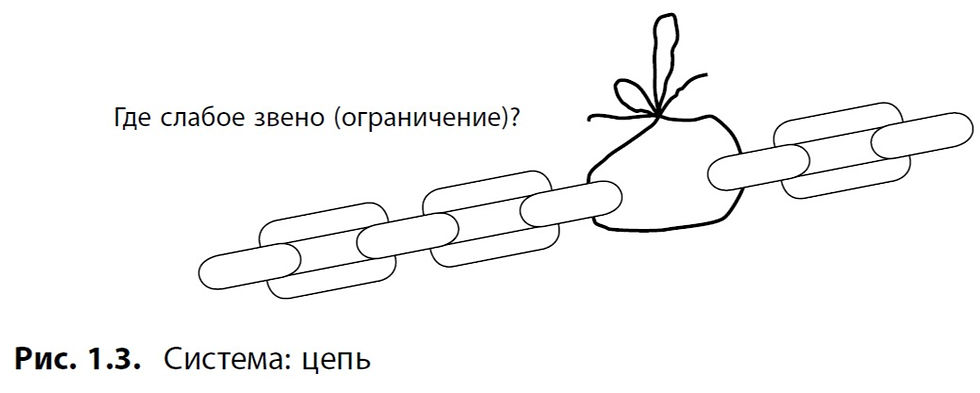
For example, reduce the productivity of the sales department due to the fact that the current limitation is production capacity. Production does not have time to process and release all taken orders, and raw materials are purchased for them. As a result we get:
the warehouse of raw materials and semi-finished products is overloaded, it is necessary to increase the volume of warehouse space = increased rental or construction costs, additional personnel
raw materials begin to be stored longer in the warehouse = an increase in the volume of frozen working capital and future losses. Raw materials will be stored longer, and some of them will be wasted
there will be order cancellations = reputational losses, risks of penalties + raw materials either for recycling or for “eternal storage”, due to defects or due to the inability to apply to other orders
deterioration in the KPIs of the sales department and managers = conflict between departments
emergence of "urgent" and important orders = interference with the production cycle and a decrease in productivity, which leads to an avalanche effect
increased pressure from owners on production = worsening microclimate and increased turnover.
As you can see, a huge amount of losses are generated. We'll talk more about them in the post about Lean Manufacturing. And they lead to a “perfect storm” and crisis. This example is taken from real life.
Over the course of the year, the company changed 8 production managers and 90% of the production staff, and the risk of penalties of 20 million rubles arose. And the limitation here was in the leaders.
If we return to our topic - digitalization, then the theory of system limitations will help you understand where exactly to initially introduce digital technology.
And this will make it possible to quickly see and feel the effect for little money. Which in turn will remove resistance from you and your team and will increase the amount of available finance for further changes.
Well, in the end, this will increase your net profit.
There are 5 stages in TOC - “focus stages”. If you follow these steps, you will most effectively remove the restrictions that exist in your business.

Step 1: Find the constraint
A constraint is a bottleneck, resource (human or material) or condition that impedes development. There are two types of restrictions: internal and external. The first includes factors that limit growth from within - production throughput (producing a set amount of product per day - no more, no less) or unskilled employees. External factors include market factors (intense competition, capacity, the influence of the political situation on the purchasing power of the population, etc.).
During the first stage, you need to identify the limitation. You can know it, or you can use brainstorming , TRIZ , flowcharts, thinking or mental maps , etc.
There is a production facility that produces products on machines. The limitation is a problematic machine that produces 8 units of product, which is the lowest figure. It is possible to increase production by improving the performance of other machines, but this will not remove the limitation. Therefore, the task is to decide how to use this machine effectively.
Step 2: Decide how to make the most of the constraint
Obviously, in a particular case, the main task is to increase the efficiency of a given machine. To do this, you need to develop rules so that it is always repaired on time, is constantly loaded, and preventive maintenance is carried out. In other words, we need a set of measures that will minimize the negative aspect. In production conditions, it is not always possible to completely eliminate the problem - if the problem was an incompetent worker, he could be fired and a better professional hired in his place, but in the case of material resources, for example, there may be certain restrictions. Therefore, this step is tied to how to use the restriction.
Step 3. Manage through the constraint
The focus of management attention should be directed to the problematic machine. It is necessary to monitor its work constantly, since it sets the rhythm for the entire system. Already at this stage, the first results should appear: productivity, if everything was done correctly, will increase.
Step 4: Expand the constraint
After improving the problematic parameter (for example, the machine began to produce 12 units instead of the initial 8), you need to think about whether the process can be improved further.
Step 5. Return to first step
Returning to the beginning of the algorithm means searching for a new constraint - the most pressing problem under new conditions. This is how a new stage of business improvement begins.
One of the methods of the theory of constraints, widely used in the field of production, is the “drum-buffer-rope” method, which sets the following principles:
The drum is your limitation, on which the maximum productivity of the entire enterprise or division depends. All elements must obey the rhythm of the constraint at which it has maximum performance
buffer - a supply of materials and time that ensures constant operation of the drum.
“Rope” is how you organize the flow of materials to the drum: how you plan, how you exchange information. That is, this is about the process of operational planning, creating a pull system so as not to fall into overload and crisis
Ultimately, you must build an operating rhythm that ensures maximum drum performance: it always has resources, but it is not overloaded.
Critical chain
The critical chain method (MCM) was also described by E. Goldratt, but somewhat later than the Theory of Constraints, in 1997.
It is a tool for planning and managing projects, indicating their dependence on resources, risks and uncertainties. The description of the method is quite complex, so we will try to simplify it as much as possible.
The three main factors in most problems are: multitasking, student syndrome and Parkinsoa's law.
Almost everyone has experienced poor multitasking. This is when we start one thing, then abandon it, starting to work on something more significant at that moment, and later we leave this task unfinished. This each time leads to loss of time and efficiency, because you need to “get back into work” again. Student syndrome is a common procrastination, characteristic of many is the habit of procrastinating and starting to complete a task at the last moment. Parkinson's Law is the observation that work takes up all the time allotted to it.
The critical chain method allows you to deal with these factors. The first requirement is to reduce multitasking so that employees are focused on the tasks at hand. Secondly, Parkinson’s law should not be neglected. It is worth remembering that even if the project was completed ahead of schedule, there will be work to improve it, which will still lead to its delivery on time or even later. Because of this, one may get the impression that the time frame was initially set correctly.
The theory of constraints also offers a more general approach to finding and removing constraints, which can be applied not only in production.

The approach consists of the sequential construction of analytical schemes of the following types:
Current reality tree - to identify cause-and-effect relationships between adverse events and the root cause of most of these adverse events


Conflict Resolution Diagram (CRD) - To resolve contradictions and hidden conflicts in a system, which are often the cause of chronic problems in the system. The method of eliminating contradictions is usually called injection

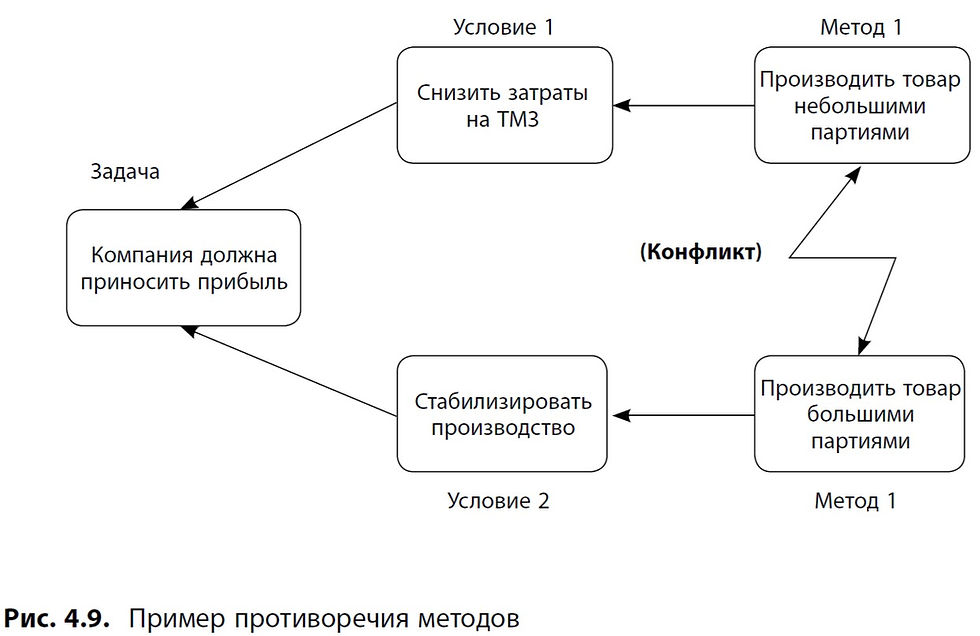
Future reality tree (FRT) - when certain methods (injections) are selected to eliminate the root causes of problems or conflict identified using FRT in the conflict resolution diagram, a tree is built showing the future state of the system. This is necessary to identify the negative consequences of the selected injections ( negative branches ) and select ways to combat them.


Transition tree - to identify possible obstacles to transformation and eliminate them.



Change plan - to develop specific instructions for performers to implement planned changes.

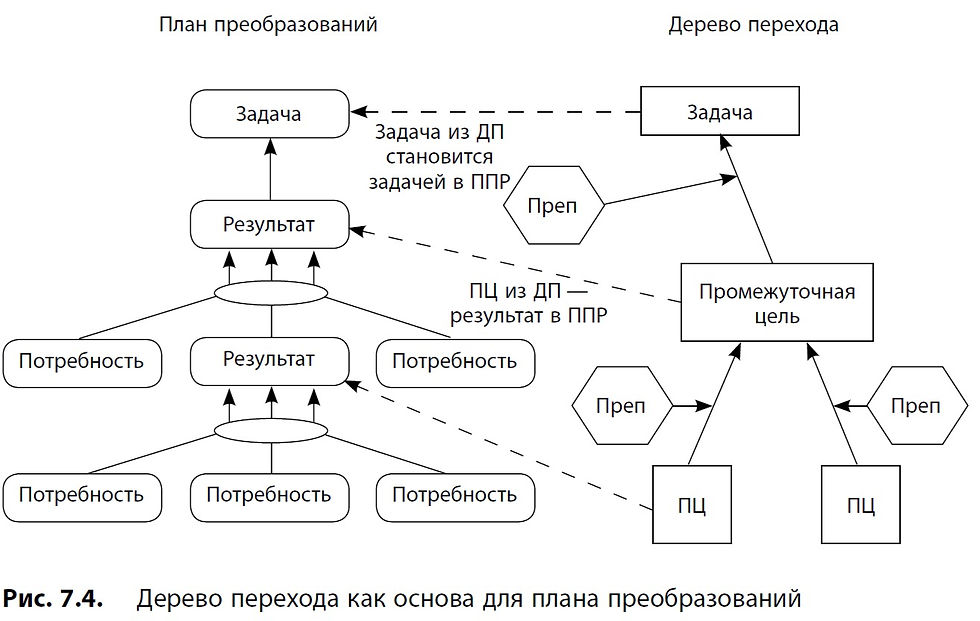

This approach is described in artistic form in the book “ Goal-2. It's not about luck ." In more formal academic language - in the book by W. Detmer “ Goldratt's Theory of Constraints. A systematic approach to continuous improvement ."
Goldratt's method of thought processes, unlike many similar information visualization techniques (for example, Ishikawa diagrams , mental maps ), offers a set of rules that allow you to check the presence of cause-and-effect relationships and their reliability. Such rules are called criteria for verifying logical constructions (CPLP, Categories of Legitimate Reservation) - these are eight provisions with which you can check, prove or disprove the correctness of the established cause-and-effect relationships:
Clarity —everyone clearly understands the statements used in the diagram.
Having a statement - a statement contains a complete thought.
The existence of a cause-and-effect relationship - does the named cause actually cause the indicated effect?
Sufficiency of the given cause - the given cause is sufficient to cause the specified effect, in the given context.
Checking for the presence of an alternative cause - could the named cause be just one of the possible ones?
It is inadmissible to replace cause with effect —cause and effect are confused.
Search for a verification effect - if the named cause occurs, then it must have not only the indicated effect, but also some other, side effects (which do not necessarily have to be indicated in a specific diagram).
Absence of tautology - the effect is offered as a justification for the existence of the cause

In general, restrictions can be divided into:
external (excessive productivity) and internal (insufficient productivity);
material and intangible.
Goldratt himself identified the following types of restrictions:
Physical - lack of materials, space, necessary people.
Political constraints are informal guidelines of “this is how we work” or formal rules and regulations, for example from the state, that limit the ability to act.
Paradigm limitations are ingrained habits and ways of thinking and decision making. That is, these are not external restrictions, even cultural ones, but internal ones. An example is the personal effectiveness of a leader, the limitations of his knowledge and resources: the ability to critically approach priorities, skills in setting tasks, concentration, attention, time to pay attention, etc. And in our practice, it is often managers who limit the productivity of their departments.
Market Constraints - Your productivity is higher than the market. This happens either at the start of a business and the market doesn’t need you, or vice versa - the product and market match. As a result, they successfully scaled and took over the entire market. This is the ultimate limitation you will face
Try to answer the questions from the illustrations below


1. Solving only one, two, three restrictions and abandoning further development
It is necessary to avoid stabilizing the state after removing the next restriction. Constant hunger is required, improvement is a continuous cycle.
If all is well, the system may be slipping into an inert state, resulting in slow destruction. The Kaizen philosophy will help you, which is precisely aimed at introducing a culture of continuous improvement.
2. Narrow focus
For example, you can pay attention to key product metrics - conversion, revenue, and so on. But at the same time, ignore such things as the number of staff, physical space, market restrictions, and so on. You need a systemic view of your work processes and product, a “look down” or “helicopter vision”. The more restriction areas you monitor, the better. To do this, it is useful to know what restrictions there are.
The theory of system limitations works well both as an independent tool and as an element of a systems approach
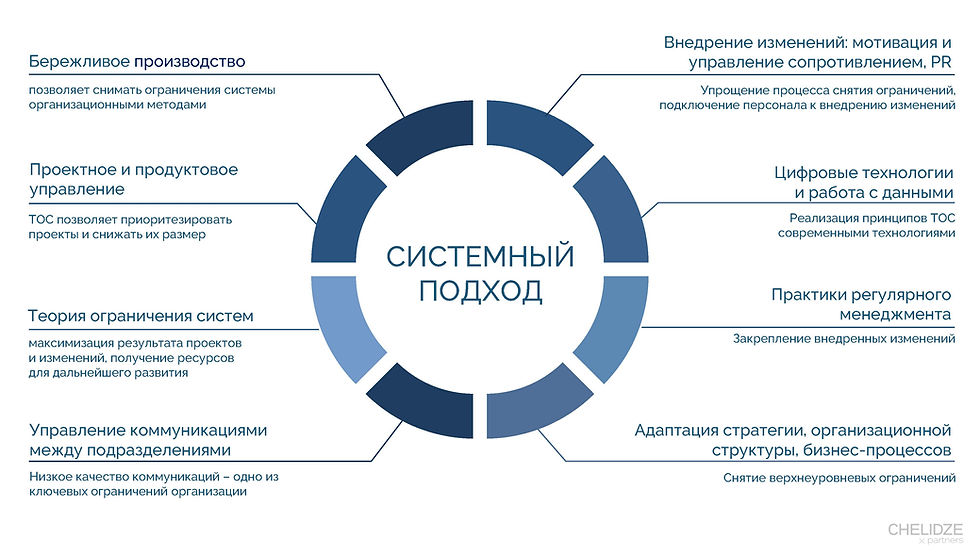
When combined with lean manufacturing, project and product management, digitalization and digital transformation, true synergies can be achieved. It is one of the elements of your management system.

Links: