Lean Production. Part 1
- Джимшер Челидзе
- May 31, 2024
- 31 min read
Updated: Jul 8, 2024
Content:
This is the first post in a series, the second is available here
Lean manufacturing (LP, lean production, lean manufacturing ) is a management concept based on the constant desire to eliminate all types of losses. It involves the involvement of each employee in the optimization process and maximum customer focus. This is an interpretation of the ideas of the Toyota Production System (TPS), which initially produced low-quality cars and then surpassed American manufacturers in both quality and price. The essence of the concept was superimposed on the concept of “ 6 sigma ” and the result was “lean+6 sigma”.
The power supply system saved Porshe from bankruptcy and is the main production system of the world's largest companies.
For a deeper dive, we recommend reading “The Toyota Way. 14 Management Principles of the World’s Leading Company” by Jeffrey Liker and taking “ Lean Manufacturing. Basic Course ”
Part 2 is available here
Lean manufacturing allows you to unlock the potential of the implemented digital technologies, provide a synergistic effect, prevent the causes of personnel resistance and reduce the cost of maintaining the implemented IT systems by 50-80%.
Toyota Tao - the basic “commandments” that underlie TPS. This is something like the 10 commandments from the bible
DAOs are divided into 4 groups:
1. Long-term philosophy;
2. The right process produces the right results (we're talking about using a range of TPS tools)
3. Add value to the organization by developing your employees and partners;
4. Constantly solving fundamental problems stimulates lifelong learning.
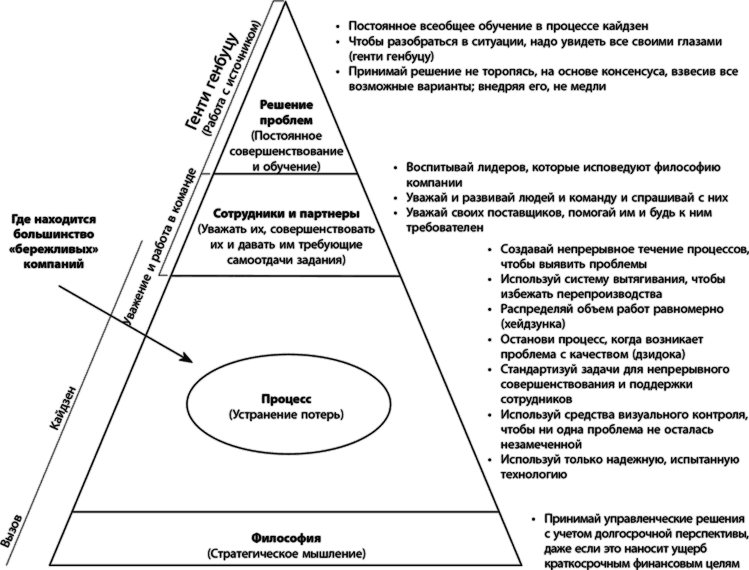
Section I. Long-term philosophy
Principle 1: Make management decisions with a long-term perspective, even if this is detrimental to short-term financial goals.
Use systematic and strategic approaches when setting goals, and all operational decisions should be subordinated to this approach. Realize your place in the history of the company and try to take it to a higher level. Work on the organization, improve and rebuild it, moving towards the main goal, which is more important than making a profit. A conceptual understanding of your purpose is the foundation of all other principles.
Your main task is to create value for the consumer, society and the economy. When assessing any type of activity in a company, consider whether it solves this problem.
Be responsible. Strive to control your destiny. Believe in your strengths and abilities. Be accountable for what you do, maintain and improve the skills that allow you to produce added value.
Section II. The right process produces the right results
Principle 2: A continuous flow process helps identify problems.
Reengineer your process to create a continuous flow that effectively adds value. Minimize the amount of time unfinished work sits idle.
Create a flow of products or information and establish connections between processes and people so that any problem is identified immediately.
This flow must become part of the organizational culture, understandable to everyone. This is the key to continuous improvement and development of people.
Principle 3: Use a pull system to avoid overproduction.
Make sure that the internal consumer who accepts your work gets what he needs at the right time and in the right quantity. In a just-in-time system, the inventory of products must be replenished only as they are consumed.
Minimize work in progress and inventory storage. Keep a small number of items in stock and replenish these stocks as customers pick them up.
Be sensitive to daily fluctuations in consumer demand, which provide more information than computer systems and charts. This will help avoid losses due to the accumulation of excess inventory.
Principle 4. Distribute the workload evenly (heijunka): work like a tortoise, not like a hare.
Eliminating waste is only one of three conditions for lean manufacturing success. Eliminating overload of people and equipment (muri) and uneven production schedules (mura) are equally important. This is often not understood in companies that are trying to apply lean principles.
Work to distribute the load evenly in all processes related to production and service. This is an alternative to alternating rush jobs and downtime, characteristic of mass production.
Principle 5: Make stopping production to solve problems part of the production culture when quality requires it.
Quality for the consumer determines your value proposition.
Use all available modern quality assurance methods.
Create equipment that can independently recognize problems and stop when they are identified. Develop a visual system to notify the team leader and team members that a machine or process requires their attention. Jidoka (machines with elements of human intelligence) is the foundation for “embedding” quality .
Ensure that the organization has a support system in place to quickly resolve problems and take corrective action.
The principle of stopping or slowing down the process should ensure that the required quality is obtained “the first time” and become an integral part of the company’s production culture. This will improve process productivity in the long term.
Principle 6: Standard tasks are the basis for continuous improvement and delegation of authority to employees.
Use stable, repeatable work methods to make results more predictable, improve teamwork, and produce more consistent output. This is the basis of flow and pull.
Capture the accumulated knowledge about the process, standardizing the best methods at the moment. Do not discourage creative expression aimed at raising the standard; consolidate what you have achieved with a new standard. Then the experience accumulated by one employee can be transferred to the one who replaces him.
Principle 7. Use visual inspection so that no problem goes unnoticed.
Use simple visual aids to help employees quickly identify where they are meeting the standard and where they have deviated from it.
You should not use a computer monitor if it distracts the worker from the work area.
Create simple visual control systems in your workplace that promote flow and pull.
If possible, reduce the length of reports to one sheet, even when it comes to major financial decisions.
Principle 8: Use only reliable, proven technology.
Technology is designed to help people, not replace them. It is often worth doing the process manually first before introducing additional hardware.
New technologies are often unreliable and difficult to standardize, jeopardizing flow. Instead of using untested technology, it is better to use a known, proven process.
Before introducing new technology and equipment, testing should be carried out under real-life conditions.
Reject or change technology that conflicts with your culture and may undermine stability, reliability, or predictability.
Still, encourage your people to keep an eye on new technologies when it comes to finding new ways. Quickly implement proven technologies that have been tested to improve flow.
Section III. Add value to the organization by developing your employees and partners
Principle 9. Develop leaders who thoroughly know their business, profess the company's philosophy and can teach it to others.
It is better to develop your own leaders than to buy them from outside the company.
A leader must not only complete the tasks assigned to him and have the skills to communicate with people. He must profess the company's philosophy and set a personal example of how to do business.
A good leader must know the day-to-day work like the back of his hand, only then can he become a true teacher of the company's philosophy.
Principle 10: Develop exceptional people and build teams that embrace the company's philosophy.
Create a strong, sustainable work culture with lasting values and beliefs that everyone shares and accepts.
Train exceptional people and teams to operate with a corporate philosophy that produces exceptional results. Work tirelessly to strengthen your production culture.
Form cross-functional teams to improve quality, productivity and flow by solving complex technical problems. Arm people with the tools to improve the company.
Relentlessly train people to work as a team towards a common goal. Everyone should learn to work in a team.
Principle 11: Respect your partners and suppliers, challenge them and help them improve.
Respect your partners and suppliers, treat them as equal participants in a common cause.
Create conditions for partners that stimulate their growth and development. Then they will understand that they are valued. Set challenging tasks for them and help them solve them.
Section IV. Constantly solving fundamental problems stimulates lifelong learning
Principle 12. To understand the situation, you need to see everything with your own eyes (genchi genbutsu).
When solving problems and improving processes, you must see what is happening with your own eyes and personally verify the data, and not theorize by listening to other people or looking at a computer monitor.
Your thoughts and reasoning should be based on data that you have verified yourself.
Even representatives of the company's senior management and department heads must see the problem with their own eyes, only then the understanding of the situation will be genuine and not superficial.
Principle 13. Make a decision slowly, based on consensus, after weighing all possible options; when implementing it, do not hesitate (nemawashi).
Do not make a definitive decision on a course of action until you have weighed all the alternatives. When you have decided where to go, follow the chosen path without delay, but be careful.
Nemawashi is a process of collaborative discussion of problems and potential solutions in which everyone participates. His task is to collect all the ideas and develop a common opinion on where to move next. Although this process takes quite a lot of time, it helps to carry out a larger search for solutions and prepare conditions for the prompt implementation of the decision made.
Principle 14: Become a learning structure through relentless self-reflection (hansei) and continuous improvement (kaizen).
Once the process has stabilized, use continuous improvement tools to identify the root causes of inefficiencies and take effective action.
Create a process that requires almost no inventory. This will help identify wastage of time and resources. When waste is obvious to everyone, it can be eliminated through continuous improvement (kaizen).
Protect the knowledge base about the organization of your company, prevent staff turnover, monitor the gradual promotion of employees and the preservation of accumulated experience.
When you complete the main stages and complete the entire work, analyze (hansei) its shortcomings and speak openly about them. Develop measures to prevent the repetition of mistakes.
Instead of reinventing the wheel when you start a new job or when a new manager comes on board, learn to standardize best practices and methods.
Below is a file with a short, 1-page, and full version of the memo
Lean manufacturing is based on 4 principles:
1. Determine the value of a specific product
In general, the Japanese are very fond of the value-based approach. This is also reflected in their project management standard - P2M . But this is understandable; they developed in conditions of limited resources, where the cost of error is too high.
Also in digital internal projects, it is necessary to clearly understand - who is the final consumer and who is the intermediate consumer? What is the value to them?
To do this, as a guideline, we focus on what losses can we eliminate?
Without this, we risk introducing changes and systems that no one wants to use, and they will simply turn into expensive toys.
2. Define the value stream for this product (from raw materials to finished product, from order to delivery, from concept to production)
This principle allows you to understand - at what points do you have problems? Where do you kill the client’s desire to cooperate with you, where do you waste resources (time and money)?
Well, what’s the point of introducing robotics in production if the client has to wait a week for order confirmation, while production itself already takes 1-2 days?
3. Ensure (optimize) the continuous flow of the product value stream
Well, this is where working with processes comes into play, eliminating all expectations and unnecessary approvals. That is, arrange the work so that it is as economical as possible and aimed at meeting the client’s needs.
4. Strive for excellence
Here we are talking about the fact that you cannot optimize / automate / digitize everything once and be done with it.
No, we need to come back and improve our processes and services over and over again. People, conditions, technologies change, and therefore processes need to be changed.
This is the basis, for example, of Kaizen. When people on the ground themselves eliminate all unnecessary actions, they improve their working conditions.
At every stage of production it is necessary to combat losses
Muda
Muda - losses, actions that do not create value for the end consumer
1. Overproduction
The most common and entails other types of losses. Producing more products and services than is needed or what the consumer can buy.
The reasons are production in large quantities, lack of knowledge of demand, lack of quick changeover.
Example: producing a large number of products, making unnecessary copies of documents, reports, long and regular meetings or planning sessions.

2. Waiting
Losses associated with people waiting for resources, technological operations, as well as equipment downtime during uneven loading, lack of necessary materials.
The reasons for the occurrence are a violation in the logistics system, equipment breakdown, lack of instructions from management, lack of planning.
Example: equipment downtime until processing at the previous stage is completed, the employee waits for instructions
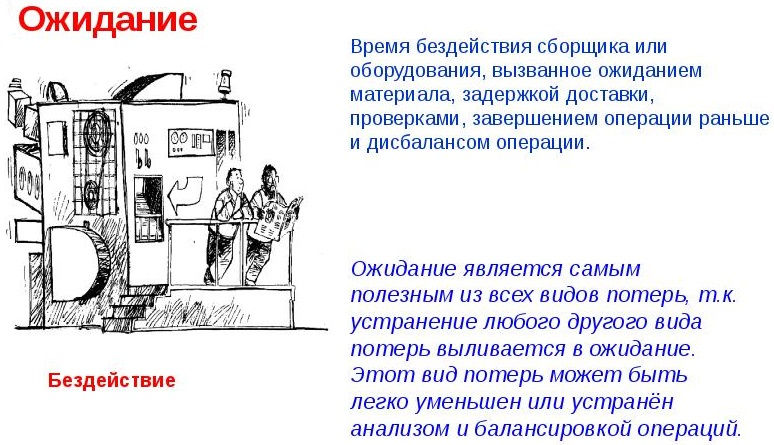
3. Inventories
Purchasing and storing excess amounts of materials that are not yet needed. Excessive reserves freeze money. This type of loss hides production planning problems and process unevenness.
The reasons for the occurrence are uneven production, demand for products is not taken into account, which leads to excess stocks of finished products, poorly established relationships with material suppliers.
Example: storing a large volume of materials that is necessary for production for six months, without taking into account the cost of maintaining a warehouse, producing Christmas tree decorations in excess of seasonal demand and stocking the warehouse, leading to increased costs
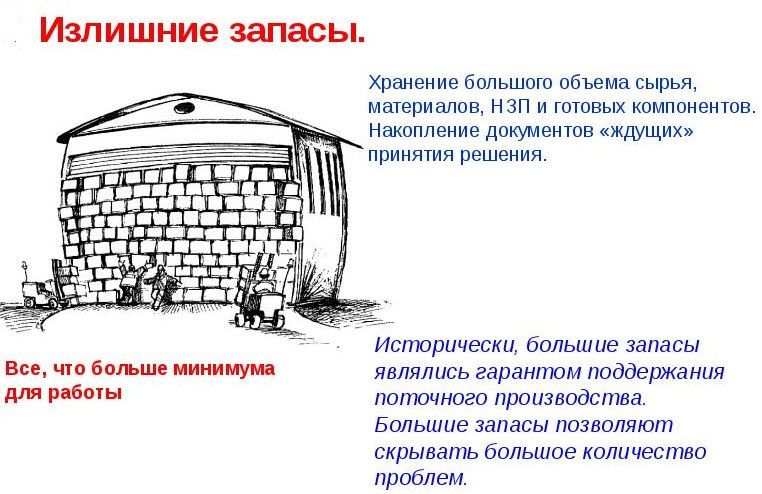
4. Unnecessary transportation
The movement of materials or goods between departments that do not add value to the final product or service.
The reasons for the occurrence are irrational use of production space, unnecessary intermediate storage areas, inconvenient placement of equipment.
Example: location of the spare parts warehouse and production at a greater distance from each other
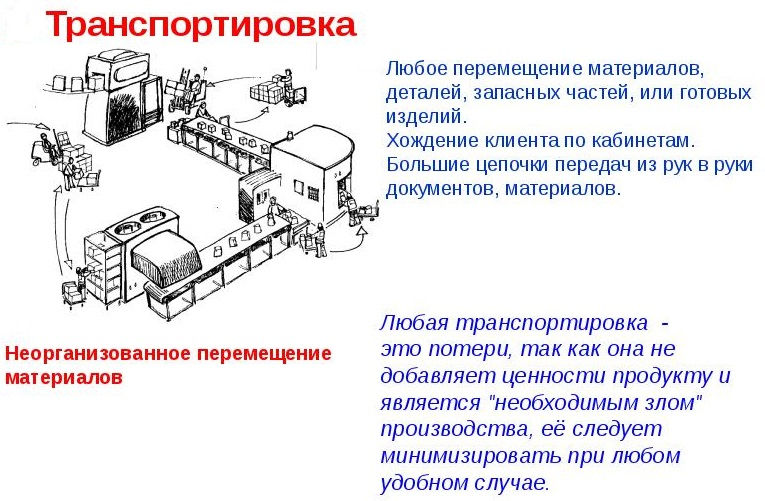
5. Unnecessary movement of people
Unnecessary movements of personnel or chaotic organization of workplaces.
The reasons for its occurrence are irrational organization of the workspace, lack of work standards, lack of visualization, violation of labor discipline.
Example: searching for the necessary tools for work throughout the entire site, lack of knowledge of the areas of responsibility of employees and walking around, finding out who should perform this or that operation, lack of visual standards that make it easier to find the necessary tools and materials

6. Marriage
It occurs in the process of releasing a product or service that does not meet the customer’s requirements, which entails their rework, the use of unnecessary resources and time costs.
The reasons for the occurrence are the lack of control at different stages of the production process, the lack of a built-in “Fool-Protection” system (Poka-yoke), a mismatch between the employee’s qualifications and the functions performed, or problems with equipment.
Example: when an equipment failure is detected late, a number of defective products are produced, an unskilled worker made incorrect calculations in the report
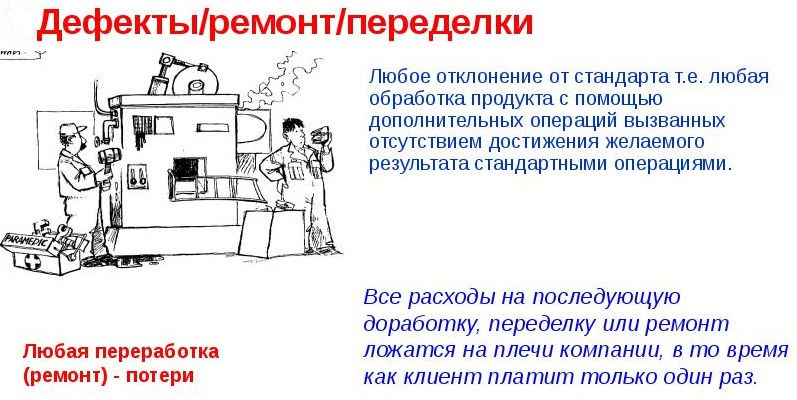
7. Overprocessing
They arise as a result of the production of products or the provision of services with qualities that the consumer does not need and is not willing to pay for them.
The reasons for this are unstudied demand or lack of incoming information.
Example: a TV remote control with a set of additional functions that the consumer does not need, making multiple copies of documents when only one is needed
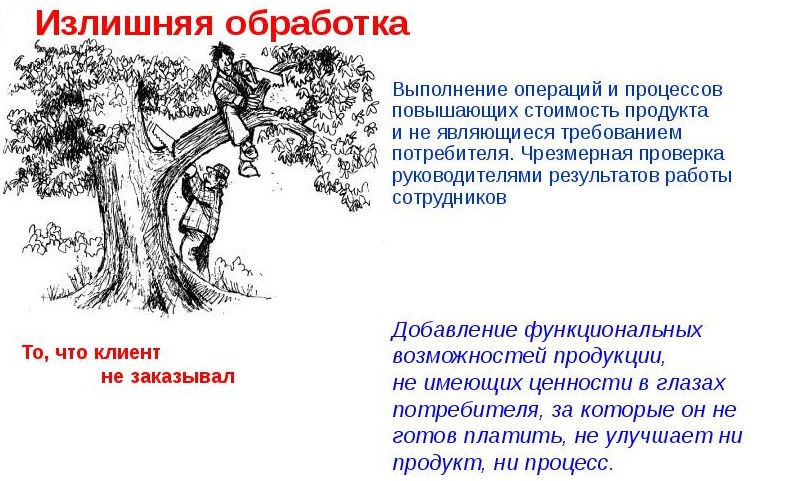
8. Untapped human potential
Unused or unrealized human potential is the exclusion of an employee’s personal qualities, knowledge, skills and abilities from the work he performs. Losses of unrealized human potential most often occur when an employee is expected to exclusively perform routine operations, the manager does not listen to subordinates, if any activity is strictly regulated by internal standards, rules or job responsibilities.
The reasons for its occurrence are an ineffectively built motivation system, competition among staff, excessive control by management, lack of motivation for taking initiative.
Example: an employee performing non-core tasks, an employee performing tasks for several employees, as well as training an employee on what he will not need in his work at all or in the near future.

Losses also occur in the office

Well, in the end, you can make a summary table with examples of losses in production, office and IT
Type of loss | Examples of waste for production, office work and IT systems |
Overproduction |
|
Expectations |
|
Reserves |
|
Unnecessary transportation |
|
Unnecessary movement/movement of people |
|
Marriage |
|
Overprocessing |
|
Untapped human potential |
|
How Toyota is working to eliminate waste using modern technologies and artificial intelligence in the video below (excerpt from 07:39 to 11:31)
There are 1 and 2 types of muda:
Type 1 are actions that do not create value, but which cannot be avoided. For example, transportation, paperwork. They cannot be removed from the process, but efforts must be made to reduce them.
2 types are actions that do not create value at all, and they can and should be excluded from the process completely. For example, waiting, inventory, defects, etc.
Moore
Mura - unevenness. When demand is uneven, queues form and execution time increases. Additional materials and supplies are required to meet peak demand. Working in emergency mode tires people and reduces their efficiency and quality of work.
Muri
Muri - overload of people or equipment. We push machines or people to their limits. Overloading people threatens their safety and causes quality problems. Overloading equipment leads to accidents and defects.
These 3 "M" represent a single system.
Often the root of the problem is "Mura", since unevenness leads to overload of "Muri", which in turn generates many other losses.


Video:
Kaizen is a Japanese philosophy that focuses on continuously improving processes in small steps.
Its essence is that local performers know best what can be improved in their work.
For this to work you need:
constantly collect feedback and implement changes; if they are not applicable, then it is necessary to explain to the initiator what exactly is wrong?
people need to be trained so that they don’t just send wishes and waste time on long conversations.
This not only improves processes, but also motivates employees.
In our practice, the best initiatives came from the “grassroots”
Examples:
1. During production, defects may occur or the entire order may not be completed: they didn’t have time, the parts didn’t arrive. As a result, the packers spent a long time explaining the details to the production manager, and he to the planning and sales department.
The solution from the packers is to put a number on each part in the drawing itself. Implementation in 1C - a couple of days.
Eventually:
planners simply handed over reports and drawings
the planner immediately knew what needed to be reordered and said when the missing part would arrive;
The sales department clearly understood when the order would be ready.
2. Feedback from operators.
By changing the location of consumables, it was possible to reduce the time for changeover between orders by 50%: there was simply no need to go to the other end of the workshop, touching other orders along the way.
Do you think the combination of this approach and digital tools will be more effective than buying expensive control systems, but causing chaos in everyday work?
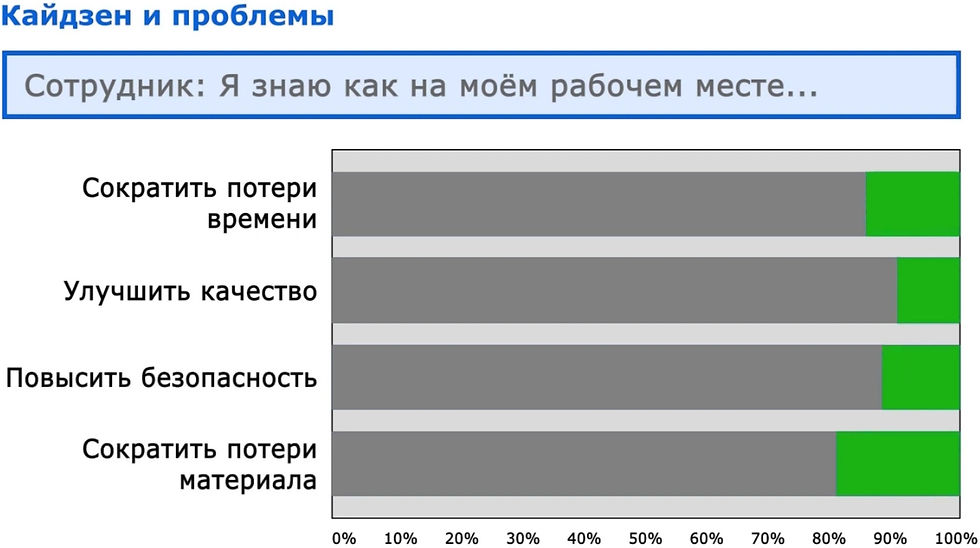

More details at this link
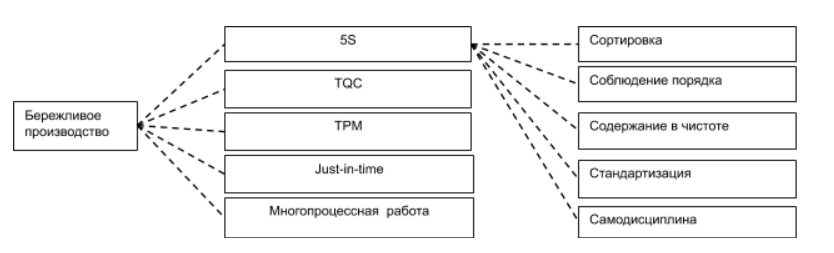
5S is a method of organizing a workplace that:
increases the efficiency and controllability of the operating area;
helps to quickly get rid of accumulated rubbish and prevent its reappearance in the future, including to prevent a new marriage;
saves time searching for “what, where?”;
improves corporate culture (we change conditions and develop new habits among people)
The Japanese believe that it is necessary to “dispel the fog”, to make sure that everything is clear, signed, and put in its place. Then all losses become visible, deviations become obvious and can be quickly corrected before becoming a problem.
If the workplace is a mess, then everything is “shrouded in fog”, where losses are born.
At the same time, the essence of the 5S system is not only to put things in order in the workplace once, but also to maintain such order at all times.
5S algorithm:
1. Sorting: all items in the workplace are divided (sorted) into necessary and unnecessary. Unnecessary items are removed from the workplace. Including in IT - everything unnecessary is removed from the system desktop.
2. Maintaining order: items are placed in places so that they are easy and convenient to use. Here we are talking about UX design.
3. Keeping it clean: all objects and the workplace are cleaned, washed, painted, dirt, dust and debris, and unnecessary graphic elements are removed.
4. Standardization: a visual standard for the arrangement of objects is drawn up: outlines of objects, signatures on their locations, cleaning regulations, desktop layouts.
5. Improvement: a system is developed for continuous improvement of previous steps and the workplace. But without standards and reference points, everything will fall into chaos.
After implementing 5S:
A large number of unnecessary items and scrap metal are removed from production workshops;
kilograms of waste paper and unnecessary trinkets are removed from office premises;
workplaces become clean and tidy.
Cleanliness and tidiness:
make equipment malfunctions obvious and improve the reliability of machines and mechanisms;
visualize quality problems and excess inventory;
minimizes the time spent searching for tools and papers;
This is a basic safety requirement.
A messy workplace leads to:
negligence at work;
industrial injuries;
equipment breakdowns and defective products.

More details at this link

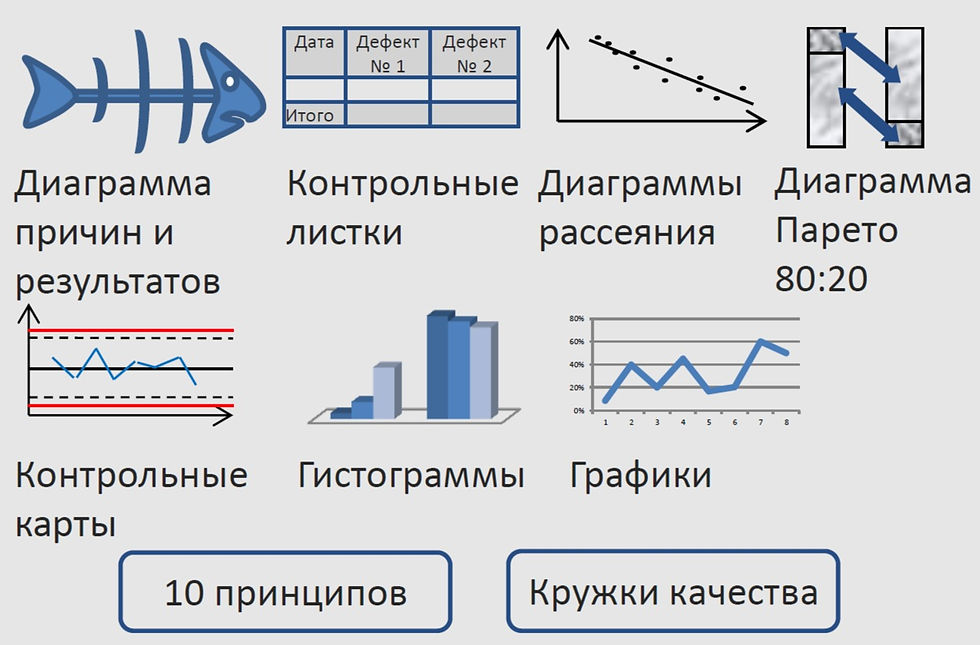
TQC (total quality control) - Total quality control.
The goal of TQC is to improve product quality by reducing the variability of product characteristics during the production process.
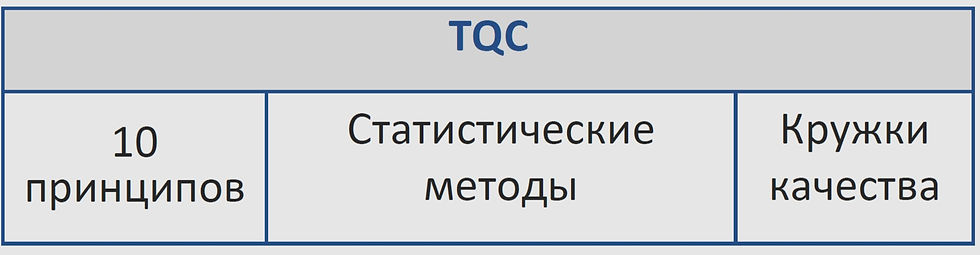
Quality mugs
In the early 1950s, the study and implementation of statistical methods of quality control began as part of TQC.
Since 1962, in Japan, to popularize the ideas of TQC, a magazine on statistical methods of quality control began to be published.
To study this magazine, Japanese enterprises began to form groups consisting of the manager and his direct subordinates:
master and workers;
head of the department and department employees.
Such groups became known as “quality circles.”
Later they began to gather not only to study statistical methods of quality control, but also to introduce ideas for improvement:
improving working conditions;
improving equipment performance;
cost reduction.
It was precisely due to the fact that all employees, and not just QCD employees, began to be involved in the quality control process that the system began to be called “universal”.
Principles of organizing Quality Circles:
1. Voluntary participation, under the supervision of a direct supervisor.
Since employees must follow the rules of the organization and the instructions of the boss, who will refuse to come to the meeting?
2. “Participation of all employees of the unit.”
The participation of all plant employees is not necessary. You can, for example, take only key production areas.
3. “2 times a month” is not very often.
Even if the meeting takes place during non-working hours, it can be paid as overtime. Therefore, this can also be an incentive to participate in it.

10 principles of TQC
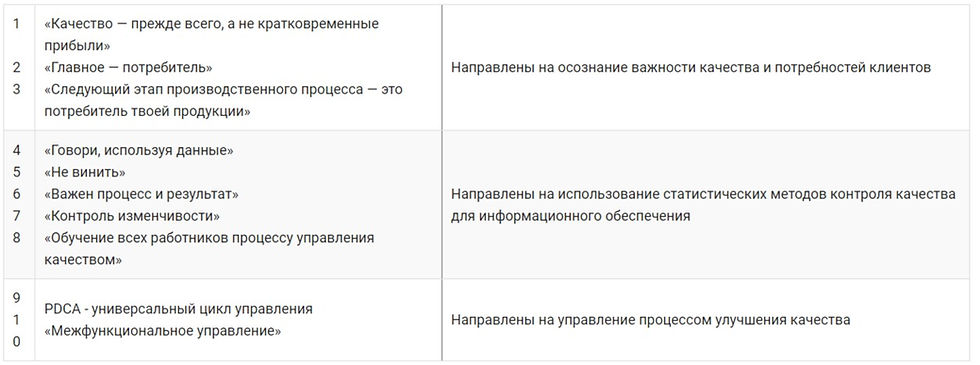
Statistical methods
"7 Basic Statistical Methods" -- are used to identify quality problems, patterns and their causes.
7 basic statistical methods:
Method 1 Cause and Effect Diagram
Method 2: Checklists
Method 3: Scatterplots
Method 4. Pareto 80:20 chart
Method 5: Control charts
Method 6: Histograms
Method 7: Charts
Using “7 Basic Statistical Methods” you can identify:
types of marriage;
reasons for marriage;
determine how quality indicators will change when parameters change;
what is the state of the production process?
Method 1: Cause and Effect Diagram

A cause-effect diagram is used to form hypotheses and find the causes of problems.
A cause-effect diagram is called an Ishikawa diagram or fishbone diagram because it resembles it in shape.
The big “bones” are usually considered to be 6 causes of defects, or 6M : materials, machines, methods, people, metrology (measurement tools), external environment.
In English, almost all of them begin with the letter "M". All hypotheses that appear during a brainstorming session are written down on the “bones” of the “fish”, and then the reasons are systematized.
The cause-effect diagram is necessary for statistical analysis, although it is not exactly a statistical method.
Method 2: Checklists

Checklists are used to collect data.
A control sheet is a piece of paper or a journal in which the values of indicators are recorded.
This is the primary information for analysis.
Method 3: Scatterplots

Scatterplots reveal relationships between two variables.
It is often important to understand how the result will change if one of the parameters is changed.
For example, by what percentage will defects decrease when the temperature or the content of harmful impurities in the metal changes?
There may be a strong relationship, a weak relationship, or no relationship between the variables.
In such a diagram, the dependence can be determined visually.
Method 4. Pareto 80:20 chart


Economist Vilfredo Pareto proved that 20% of the causes determine 80% of the result, and this law applies everywhere and in everything.
Most of the defects will be due to a small number of defects caused by a small number of reasons.
Therefore, if you identify these main types of defects and their causes, you can concentrate your efforts on them and radically improve the quality situation.
To build a chart, you need to sort the indicator values from largest to smallest.
It will inevitably turn out that 20% of the reasons lead to 80% of the defects.
This diagram allows you to set priorities and further identify the most likely causes of marriage.
The 80/20 ratio is most common, but is not required. It is quite possible that, according to the results of the analysis, it will be 70/30 or 90/10.
Method 5: Control charts
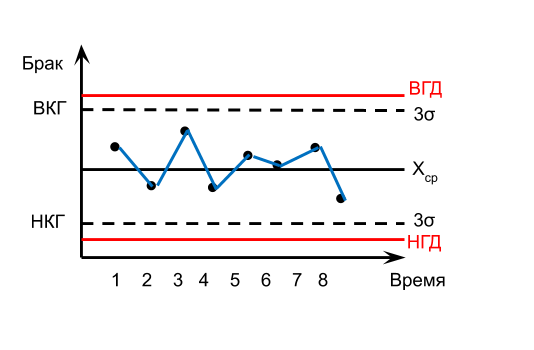
Control charts are the most complex of all the statistical methods listed.
The control chart method was proposed by Walter Shewhart in 1924.
The quality of manufactured products is subject to variation, that is, variability.
Control charts allow you to identify and eliminate certain causes of variation, thereby stabilizing the yield of quality products.
A control chart consists of a center line and two control limits: upper and lower. To calculate the upper and lower bounds, 6 sigma calculations are used.
If the indicator values are within the control limits and do not show a trend, then the process is considered controlled; if the values are outside the control limits, then the process is considered uncontrolled.
Thus, the map allows you to identify the state of the process and trends, and identify the causes of deviations.
Method 6: Histograms
If all 6M factors remained unchanged, the result would be unchanged.
In practice, we are dealing with changing factors that lead to changes in the result and its distribution.
The histogram allows you to determine what the distribution of the result looks like during the manufacture of a product.
Method 7: Charts
Graphs greatly simplify the perception of statistical information.
MS Excel contains a large number of different chart options for visual presentation of information.
The main idea of TQM ( Total Quality Management) is that the company should work not only on product quality, but also on the quality of work organization in the company , including the work of personnel. Constant parallel improvement of 3 components:
product quality
quality of process organization
personnel qualification level
This allows you to achieve faster and more efficient business development.
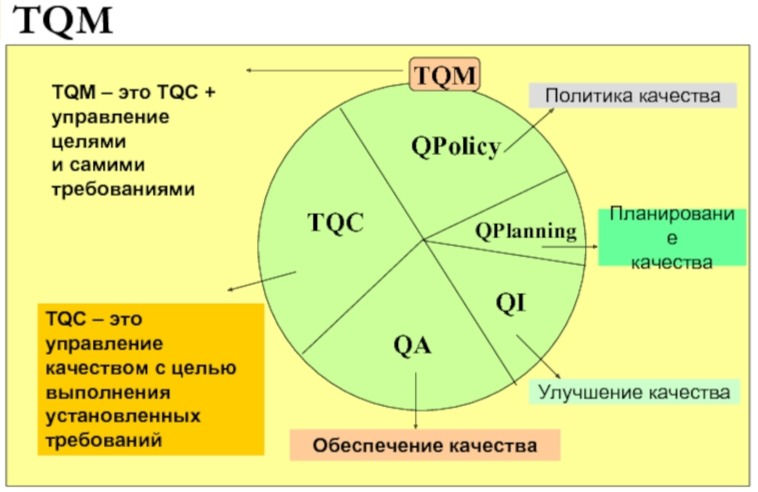
Quality is determined by the following categories:
degree of implementation of customer requirements
values of the company's financial indicators
level of satisfaction of company employees with their work
The principle of TQM can be compared to holding a ball on an inclined plane. To prevent the ball from rolling, it must either be supported from below or pulled from above.
TQM includes 2 mechanisms:
Quality Assurance (QA) - quality assurance - maintains the required level of quality and consists of the company providing certain guarantees that give the client confidence in the quality of a given product or service.
Quality Improvements (QI) - quality improvement - suggests that the level of quality must not only be maintained, but also increased, correspondingly raising the level of guarantees.
Two mechanisms: quality control and quality improvement - allow you to “keep the ball in the game”, that is, to constantly improve and develop the business.
TQM is based on the following principles:
customer orientation
involvement of employees, which allows the organization to profitably use their abilities
approach to the quality system as a system of business processes
systematic approach to management
continuous improvement
There are 5 deadly diseases that must be eliminated from an organization to successfully implement TQM. If left unchecked, these 5 deadly diseases can not only hinder the implementation of TQM, but also gradually destroy the organization. These are the 5 deadly diseases:
Main line control only . An organization that cares only about the main line of development and manages exclusively numbers is doomed to failure. Managing is hard work; a manager who relies only on numbers simplifies his task. Managers must know the process, be involved in it, understand the sources of problems and provide examples of their solutions to their subordinates.
Performance assessment based on a system of quantitative indicators . Appraisal that uses metrics, reports, rankings, or annual performance reviews sometimes results in classifications, forced quotas, and other rankings that create unhealthy competition and disrupt teamwork within the organization. Instead of using such systems, managers should provide personal feedback to employees' individual performance to help them improve.
Focus on short term gains . If an employee has had the experience of making quick profits in the past, he will try to continue to work in the same way. Management must convince employees that the organization should prioritize long-term, sustainable growth and improvement over short-term gains.
Lack of strategy . If the organization does not have any consistency in the goals being realized, the organization's employees will feel insecure about the possibility of their continuous professional and career growth. The organization must have a continuously implemented strategic plan, which should also include quality improvement issues.
Personnel turnover . If an organization experiences high staff turnover, this indicates serious problems. Eliminating the first 4 deadly diseases can help overcome this one. Management must take steps to make employees feel like they are an important part of a unified team rather than an isolated organization.
Links:
Total Quality Management on Wikipedia
More details at this link

TPM (Total productive maintenance) is:
General equipment care
Total production service
Total operational system
TPM is an approach to increasing the reliability and efficiency of production equipment and improving production culture.
After the successful implementation of TQC, the idea arose to use it to improve the quality of equipment operation.
TPM relies on the same principles and statistical methods as TQC.
The stability of product quality is directly related to the quality of equipment service, therefore in Japan:
in the 50s, planned repairs began to be carried out;
in the 60s, productive repairs began to be carried out;
in the 1970s, total equipment maintenance (TPM) was introduced.


The purpose of the TRM system is to reduce wasted machine time.
Basic principles of TRM:
the condition of the equipment depends on the culture of the employee;
operation and maintenance of equipment are inseparable;
the basis for work without breakdowns is a set of health-improving and preventive measures for equipment;
Maintenance is carried out by everyone (from operators and repairmen to managers)
Statistical methods for TRM
“7 basic statistical methods” in TRM are used to collect and analyze statistics of equipment breakdowns and downtime.
In this part, the TPM system is similar to the TQC system.

Statistical analysis of accidents and downtime:
allows you to identify root causes and prevent them in the future;
reduces the cost of repairs and maintenance of equipment.
When analyzing emergency downtime statistics over long periods of time, TQC statistical methods are used:
Pareto chart;
histograms;
control cards, etc.
The simplest type of downtime analysis is to build a Pareto bar chart, find the largest type of downtime on it, understand the cause and eliminate it. Then take the next largest type of downtime and deal with it the same way. And so it is with everyone.
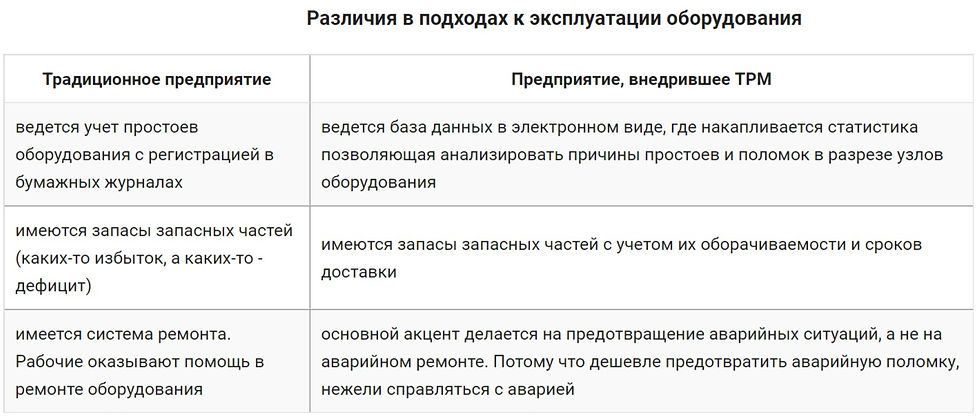
Collection of statistical data on breakdowns
Setting up a data collection and analysis system allows you to identify types of breakdowns and downtime, their causes, dynamics and regularity.
To collect information, it is necessary to develop a log form for equipment breakdowns and downtime and regulations for filling out this log.
The log may contain the following columns: No., date, shift, production line, unit, unit, part, malfunction, composition of repairs and downtime category, start and end times of downtime, start time of repairs,
and also in the log you must indicate:
actions taken;
responsible persons;
deadlines.
Analysis of information in the log allows you to determine:
reaction time of repairmen on duty;
the most common causes of breakdowns and measures to reduce them.
Computer time loss statistics
Equipment time can be divided into:
machine time that creates value;
losses of computer time that do not create value, but are inevitable and cannot be excluded;
non-value-creating wastage of machine time that can be eliminated immediately.
In the TRM methodology, there are 8 losses of computer time:
Daily Maintenance (DTO)
Scheduled preventive maintenance (PPR)
Changeover (transshipment)
Emergency downtime
Reduced processing speed
Microdowntime
Marriage
Correction of defects

The TRM system strives to reduce only: 2. PPR and 4. Emergency downtime.
Overall Equipment Effectiveness (OEE or OEE) is a special indicator for assessing the efficiency of equipment.
EEO = Equipment effective operating time (ER) / Planned equipment operating time (EUR) = 87 / 165 = 0.53
When calculating, it is necessary to take into account that unplanned time, for example holidays or absence of work in the 2nd and 3rd shifts, is not a loss of machine time from the point of view of OEO. Therefore, we are talking about losses of only planned time.
Most companies have OEO no more than 40%, the most advanced companies reach 85%.
Types and sources of losses associated with equipment
Lost time:
Stoppages due to breakdowns or failures.
The time required for adjustment, installation, for example, for replacing dies in stamping, etc.
Speed loss:
Idling due to blocking of work by sensors when the supply of parts is reduced, etc.
Discrepancy between the calculated and actual performance of the equipment.
Losses from defects
The occurrence and reproduction of defects in the process itself.
Reducing output in the period between equipment startup and reaching design loads.
Autonomous service
TRM is based on the involvement of personnel in the process of maintaining equipment in good condition.
Participants of the TRM system are equally:
managers (tools: statistical methods, autonomous maintenance, PPR);
operators - workers (tools: autonomous maintenance);
repairmen - maintenance specialists (tools: PPR),
which together ensure increased equipment reliability.
Autonomous equipment maintenance is the care of equipment by the workers who operate it.
Most problems with equipment can be resolved in advance, and as a result - a reduction in emergency downtime and costs for spare parts.
It is Autonomous equipment maintenance that distinguishes the TRM system from other repair management systems.
Operators are constantly near the equipment; they are the first to detect extraneous noise or vibration of engines, uncharacteristic creaking of drive belts and chains, oil leaks and air leaks.
Operators must know the basic parameters of their equipment and check that they are up to standard during each shift.
If the slightest deviation is detected, Operators should immediately notify the repair service, since timely identification and elimination of emerging problems is the key to preventing accidents or completely stopping expensive mechanisms.
Operators can be trained to perform many simple repairs, such as replacing bolts and hoses and adding oil and grease.
Operators must be responsible for maintaining their equipment in working order.

Production equipment must be in working order.
Autonomous maintenance by workers consists of three stages:
First stage. Equipment cleaning.
Second phase. Early detection of problems.
Third stage. Independent elimination of identified problems (equipment repair).
PPR
Planned preventive maintenance (PPR ) - aimed at preventing emergency repairs.
Proper preparation and time analysis for repairs reduces the time required for scheduled repairs.
Repairers must work closely with operators to train them on what to look for, look for, and listen for in order to identify potential problems early.
Operators and repairmen must speak the same language.
Management must ensure that preventive shutdowns are included in the production schedule for:
maintenance;
lubricants;
cleaning;
general control.
Management must ensure the timely allocation of money for repair work.
TPM and 5S work together to provide workplace safety, increased productivity and a dramatic reduction in downtime, which is so costly for the enterprise.
Visualization for TRM
Visual inspection for repairmen:
reminds you that maintenance is approaching;
informs about the results of completed repairs;
makes it easier to store tools;
makes it easier to find the necessary spare parts.
Visual safety aids:
signs about current repairs “Do not turn on, work is underway!”
hazard messages (heat, pressure, electrical voltage and toxic substances);
marking potentially hazardous areas and places of movement of forklifts and other production vehicles.
Read more about this tool at this link
Just-in-time or “Just in time” is a system aimed at receiving materials, components and finished products at the moment when it is needed.
Using the Just-in-time system you can:
reduce raw material inventories;
work in progress;
finished products.
reduce production cycle time;
reduce the batch size to the minimum economically viable (ideally to one unit of product);
balance the number of human resources;
balance the amount of equipment;
determine the performance of the current operation depending on the needs of the subsequent operation;
use audio-visual means of monitoring the condition of the product and equipment load.
Just-in-time applicable:
for the production of models of similar modifications (products of the same type);
for the production of serial rather than unique products.
where you can achieve:
grouping production operations along the technological chain of creating product families, rather than by functional departments;
production of products using small machines and well-trained operators with versatile skills;
using a mixed launch order technique (not a pipeline)

Flow Mapping
The implementation of a Just-in-time system begins with the creation of a Value Stream Map.
Value stream mapping is a fairly simple and visual graphical diagram depicting the material and information flows necessary to provide a product or service to the end consumer. A value stream map makes it possible to immediately see the bottlenecks of the flow and, based on its analysis, identify all unproductive costs and processes, and develop an improvement plan.
Mapping is a visualized description in a certain form of the flow (material, informational) of creating the value of a business process. Mapping is carried out in terms of “as is”, “as should be” and “as will be”.
A creation flow map is a lean manufacturing tool that can be used to map the material and information flows during value creation. The time to create value is considered to be the time it takes to complete the work that transforms the product so that consumers are willing to pay for it. A value stream is all the activities (value-adding and non-value-adding) needed to produce a product.



The main steps in creating a value stream map are:
Drawing up a process flowchart and layout of processes by product families.
Converting a process flowchart into a value stream map with corresponding symbols on a large sheet.
Drawing up a map of the current state, taking into account the collected data.
Data analysis and decision making.
Mapping the future state.
Making a plan to achieve a future state of flow, defining how to:
reduce what does not create value, but is necessary (Muda of the 1st kind);
eliminate that which does not create value and is unnecessary (Muda of the 2nd kind).
Current and future state of the system

Line production
Ford's method consists of a conveyor belt organization of production for a large volume of manufactured products from identical components.
When organizing production on a conveyor belt, questions arise that have no answer:
What if you need to make 100 pieces?
What if the organization’s finances are limited?
Taichi Ono argued that it is possible to produce mass products without creating assembly line production!
There are 2 ways to arrange equipment and people in production:
According to the functional principle
According to the process principle (or product or flow principle of production organization)
Principles of production organization
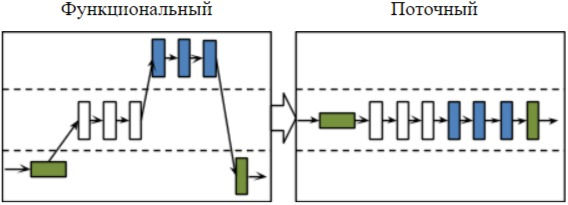
Pull production
Pull method means:
do nothing until the consumer requests it; when it requires you to do it very quickly, or
one job draws out another, or
sold a part - bought a part or shipped a product - made a product.
The sources of rhythm for the entire system are the consumer shipment schedule and takt time.
A pull system can be created for:
production;
distribution;
sales.
Pull method with the following operation:
ensures a reduction in the volume of work in progress;
controlled by a kanban system, as well as other special signals (bells, whistles and lights) to notify the need to replenish materials.
The pulling method balances:
number of human resources;
amount of materials and equipment,
in order to most fully satisfy the requirements of the consumer, both internal and external.
The pull method reduces batch sizes to the smallest possible effective quantity and has the potential to reduce it to a single product.
The pull method involves not pushing products or materials to the next stage until they are needed there.
Workers should be warned that it is completely normal to stand and wait until the next stage requires them to begin work.

Kanban system
The Kanban system (card) is a practical implementation of the JIT concept.
First used by Toyota Motor in 1972.
It took Toyota 10 years to implement it from the start of development.
Kanban - translated from Japanese means “sign”, “signal” or “card”.
Kanban is a method of providing consumers, which involves the production and delivery of products (parts, components) at precisely specified points in time, determined by the technological process and a strictly established order execution date.
Kanban is a system that allows you to produce only those products that are needed, and only in the quantity that is needed (ordered).
Kanban is a visual signal system for production.
Kanban is a system for organizing a continuous production flow that can be quickly restructured and practically does not require safety stocks.
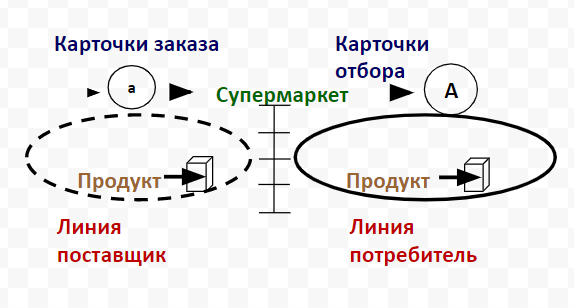
Alignment
If production orders are received in large quantities, the daily production schedule can be created using a technique called production schedule smoothing at Toyota.
Let’s assume that the plant receives orders for the next month:
8000 pieces of product A;
6000 pieces of product B;
4000 pieces of product C;
2000 pieces of product D,
the total number of orders (20,000 pieces) is divided by the number of working days in the month (let's say 20).
It turns out that every day (8 hours = 480 minutes) the company needs to do:
400 pieces of product A;
300 pieces of product B;
200 pieces of product C;
100 pieces of product D,
takt time - 0.48 minutes.
This requires changing molds four times.
SMED – quick changeover
SMED is a system for reducing the time of equipment changeover from one type of product to another (quick changeover or replacement of dies in 1 minute).
Changeover is the time it takes from the last part in the previous batch to the first part in the next batch.
The main objective of implementing SMED is to reduce changeover time and thereby increase the number of changeovers.

Equipment should be understood as:
machines;
management information systems;
instrumentation;
installations for creating prototypes;
as well as organizational units (for example: incoming control).
If reducing the changeover time by 2 times leads to a 2-fold increase in the number of changeovers, then you can:
reduce the volume of batches of materials (semi-finished products) by 2 times;
reduce the volume of finished product inventories by 2 times;
Reduce inventory turnover time by 2 times, for example, from 30 to 15 days
There is a very interesting tool in lean manufacturing - the A3 report.
This is a report that allows you to solve problems that currently have no answer.
To solve them, a working group is created, which, based on the results of the work, creates a report on a sheet of paper in A3 format that contains information about the problem and ways to solve it.
The A3 report is used to solve only an existing problem; it is not risk management.
The main essence of the idea is to describe the entire path to solving the problem on 1 sheet. When working in A3 format, you do not need to compose huge multi-page reports and 100-page plans. Especially considering that most never read it in full, especially managers. In fact, these are losses. Probably, as a result of the fight against this type of loss, the A3 format was invented to solve problems.
What is the basis
Toyota's A3 format was based on the Shewhart-Deming PDCA cycle - the basis for change management. In fact, this is one of the varieties of its visualization, but slightly adapted.
The following blocks should be placed on an A3 sheet:
1. Planning (P)
In this block we place information about the task or describe the problem that we want to solve. We describe the result we want to get, as well as the reasons that prevent us from achieving it.
2. Actions (D)
Developing an action plan that will help eliminate problems, and identifying those responsible for its implementation.
3. Control (C)
Based on the results of implementation, we monitor changes.
4. Analysis (A)
Evaluating results and formulating recommendations based on experience gained
After the first passage, the cycle closes and can be repeated an infinite number of times. In this way, the information component of A3 format is formed.

When to use A3
The A3 format is suitable for cross-functional tasks because it allows the opinions of all participants to be taken into account. Having collected all opinions and wishes, you can appoint a working group for implementation. The working group, having opinions, criteria and wishes, will be able to draw up a clear plan and begin to solve the problem.
The best way to check the quality of A3 preparation is to have it looked at by a third-party specialist. If he understands what we are talking about and what needs to be done, everything has been done correctly. The main advantage of the A3 format is that you don’t need to read the document carefully. If an outsider fails to understand, then the work is not structured correctly and you need to look for an error in the formation of task sections.
All information is placed on one sheet and should be easily understood by all members of the working group. This is the main value of the A3 format in Lean Manufacturing.
How to use?
When using A3 format in lean manufacturing, there are no clear restrictions and rules. The main criterion is convenience for the team. However, there are certain recommendations that it is advisable to follow:
The format needs to be tested by the team and the optimal form selected
The arrangement of blocks must be sequential or closed in a spiral
All text should be read unambiguously, without variability
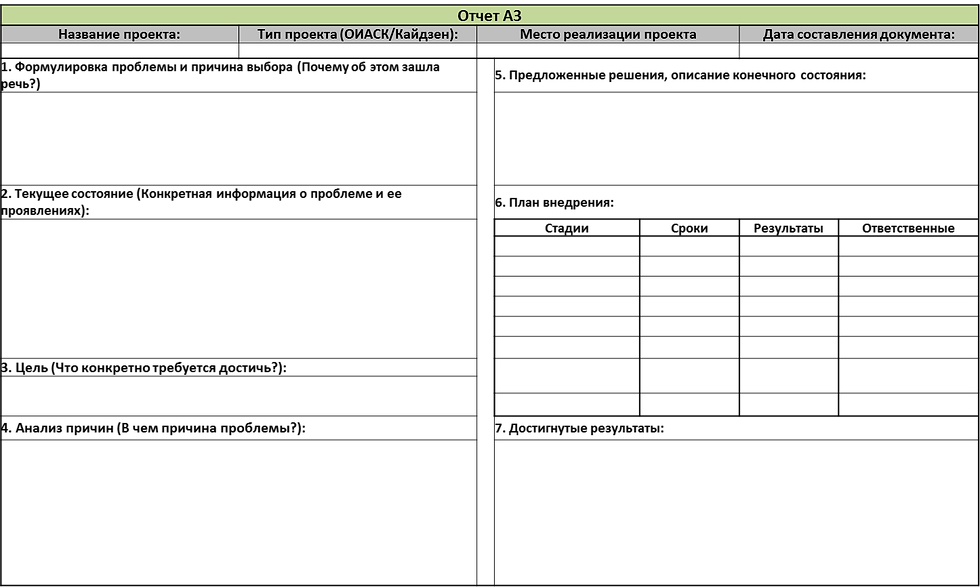

Five Whys analysis at Toyota is often used as part of a process they call “practical problem solving.” Before you begin a 5 Why analysis, you need to figure out what the problem is, or, as Toyota says, “assess the situation.”
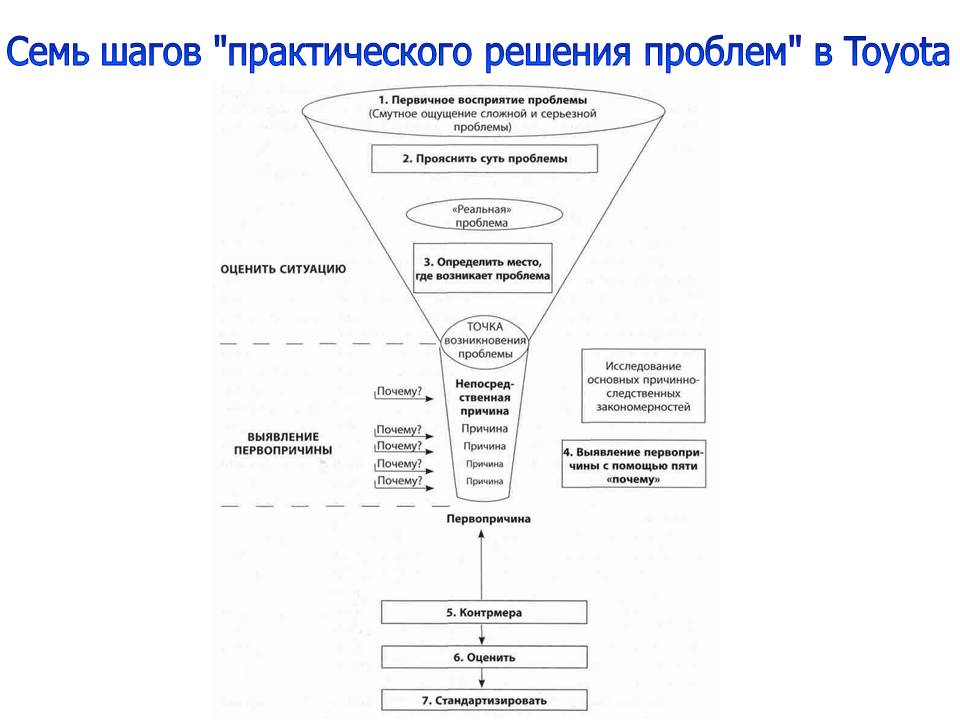
Despite the availability of various tools, techniques and metrics, the greatest importance at Toyota is given to understanding problems and solutions. Toyota says that problem solving is 20% tools and 80% thinking.
Toyota generally believes that most companies make a mistake by focusing their work only on technology.
5W1H
5W1H is a method that helps to collect information, formulate a problem and localize it. The essence of the approach is to answer 6 questions:
Who encountered the problem (who)?
What happened (what)?
When?
Where?
Why did this have to be done (why)?
How did the problem arise, as a result of what actions (how)?
Each question narrows the focus of the problem so that at the end of the 5W1H process, you will end up with a clearly defined problem with its boundaries. A clear and specific description of the problem allows you to speed up problem solving and better conduct analysis using the 5 why method.
"5 Whys" Method
“5 Whys” is a method of searching for the causes of inconsistencies that have arisen, which allows you to quickly build cause-and-effect relationships.
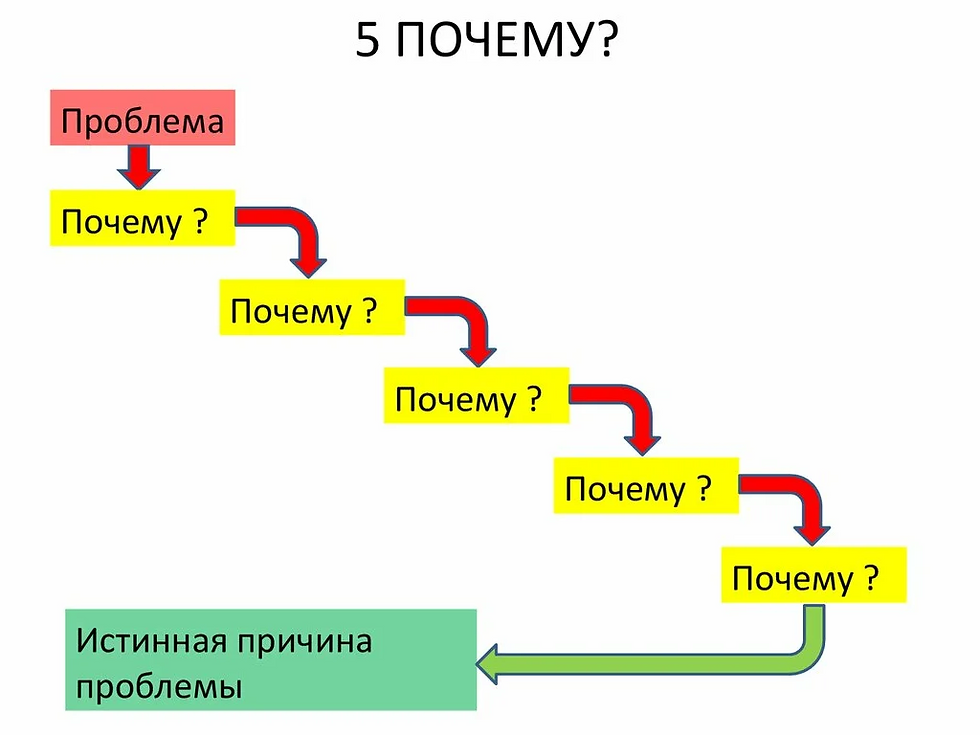

Problem: conflicts between husband and wife have become more frequent, quarrels have become more frequent, and relationships are tense.
Step 1. Why is this happening? Because the wife is offended by her husband because he pays little attention to the family.
Step 2. Why does he pay little attention to his family? Because he spends a lot of time at work and gets tired.
Step 3. Why does he spend a lot of time at work and get tired? Because there are a lot of orders and he has difficulty coping with them.
Step 4: Why is he having trouble coping with them? Because he works individually and has no assistants.
Step 5. Why are there no helpers? He didn't hire them.
The problem with this technique is that it is necessary to maintain criticality and it is easy to reach the wrong conclusions.